カシオのハイエンドラインは、日本で製造されている。工場があるのは、山形県の東根市。同社は世界中に工場を持つが、そのマザー工場が、山形カシオなのである。カシオを支える工場だけあって、そのハイテクぶりや、品質への執念はちょっと類を見ない。時計業界随一のスーパーファクトリー、その全容をご覧あれ!
Text by Masayuki Hirota (Chronos-Japan)
[2024年2月16日公開記事]
なぜ山形に工場があるのか?
山形カシオは、東根市の東根大森工業団地にある。現在この団地には17もの会社が工場や事業所を構えるが、カシオの進出は2番目とかなり早い。1979年10月に設立された山形カシオは、翌80年4月に操業を始め、時計と電卓を製造するようになった。
そんな同社に転機が訪れたのは、83年10月のこと。独自事業としてプラスティック成型と、精密金型事業に取り組むようになったのである。今や、同社の圧倒的な強みとなった樹脂の成型技術は、ここに始まったわけだ。
ちなみに最後発で時計産業に参入したカシオは、満足できる金属製のケースを入手できなかったそうだ。対して同社は、時計の世界ではまだ普及していなかった樹脂素材に注目。78年に、初めて樹脂製ケースを使った腕時計「F-100」を発売した。仮にF-100がなければ、83年の初代G-SHOCKは生まれなかっただろうし、山形カシオが樹脂の成型技術を磨き上げることもなかっただろう。
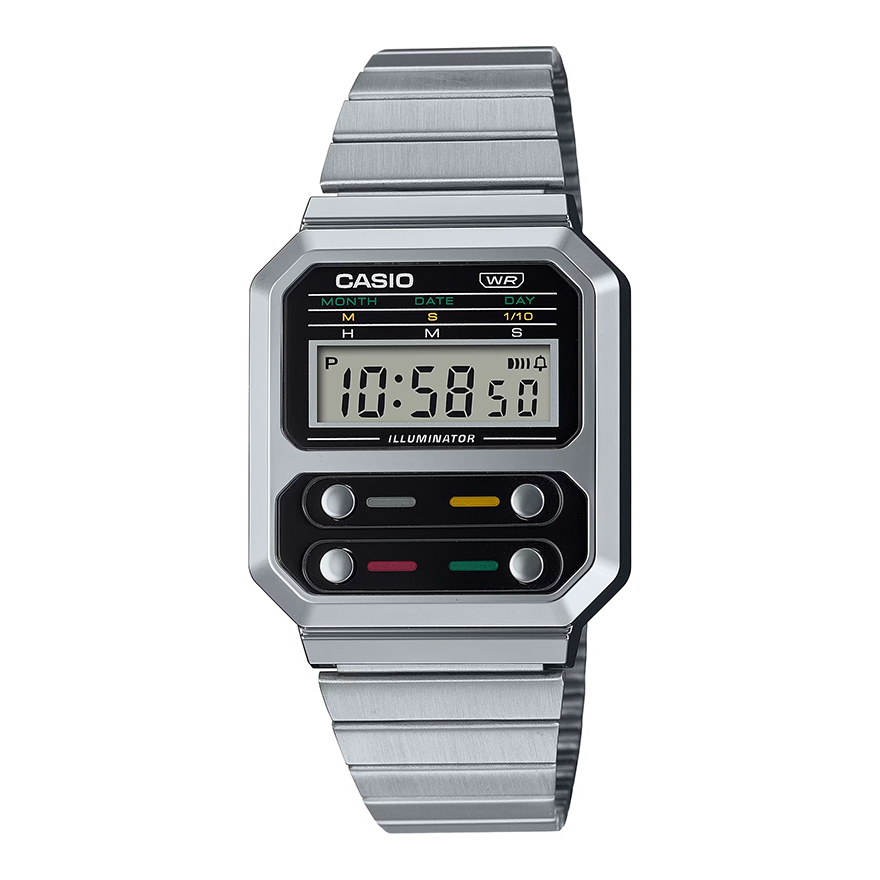
79年7月にカシオは、製造工場の甲府カシオを設立。同月には、技術開発拠点として羽村技術センターを完成させた。翌8月にはカシオ計算機(香港)有限公司を、10月には山形カシオを設立した。80年代の飛躍に向けて、大規模な投資を行ったカシオ。そのひとつの山形カシオは、やがてカシオの基幹工場となっていく。
山形カシオが、カシオの製造拠点を握っている
プラスティック成型・精密金型を皮切りに、山形カシオは事業を拡大していった。85年にはEMS事業(製造受託)を開始。86年にはFA事業、つまり工場のオートメーション化を事業化した。2004年には金型工場を建て増し拡張させ、12年には山形カシオタイを創業した。しかし、同社がカシオの中核となるには、紆余曲折があった。
1980年代に入ると、カシオは急激に海外生産の比率を増やした。その結果、海外の製造拠点は13まで増えたが、後にカシオは、外部工場に製造を委託する(EMS)方針に転換した。その割合は一時期、7割にも上ったというから、カシオは製造メーカーというよりも企画メーカーになったと言える。しかし、外部工場がより利益率の高い携帯電話などにシフトすると、製造の多くをEMSに依存していたカシオは苦境に置かれた。
対してカシオは、再び方針を転換し、製造の内製化に取り組むようになった。4拠点あった国内の工場は山形カシオに集約され(ただし山形カシオの山梨事業所はある)、海外の生産拠点も、中国3カ所、タイ1カ所に絞られた。合わせて、山形カシオをすべての製造拠点の「マザー工場」にするという方針が定められたのである。
ちなみに、海外にあるカシオの製造工場のトップは、一部山形カシオの出向者とのこと。
山形カシオ、アナログ、そしてすごい金型技術!
現在、山形カシオは基板製造のSMT、他社の開発、製造を請け負うEMS、プロジェクター、マリンスポーツ機器、ハンディターミナルなどを事業化している。しかし、その中で最も大きいのが時計部門だ。約600名の従業員中、約160人が時計部門に所属しているとのこと。
現在、山形カシオの時計部門は、すべての内製時計用モジュール(ムーブメント)を製造するほか、MR-GやOCEANUSといった高額なモデルを手掛けている。根幹にあるのは、同社の得意とする金型の製造技術だ。
現在山形カシオは、モジュールに使われる歯車などを自製するほか、金属部品に遜色ない、樹脂部品を製造するようになった。可能にしたのが、2014年に確立された、金型のナノ加工だ。
これは精密な金型で樹脂を成型するというもの。ナノ加工で成型された部品にスパッタリングで彩色を施すことで、山形カシオ製の樹脂部品は、金属部品に遜色ない仕上がりを持つようになった。例えばオシアナスの精密なインダイアル。メタル製のように見えるが、金型のナノ加工で打ち抜かれた樹脂製である。
近年カシオが採用するバイオマスプラスティックも、山形カシオの成型技術があればこそ、だ。普通の樹脂に比べて安定しにくい素材を、山形カシオは既存の素材と遜色ない精度で加工することに成功した。
今後、同社はこの技術を海外の製造拠点に移植するはずだ。
製造ラインもユニークである
山形カシオの時計部門には他社にはない、いくつかの特徴がある。ひとつは徹底した自動化だ。現在山形カシオは、基板の実装までも自動化したというから、かなりの水準にある。
まず同社は、定番モデルの製造を自動化しようと試みた。選ばれたのは「A159WA」というベーシックなモデルだ。
18年に完成したこの自動化ラインにより、製造効率は140%になったとのこと。山形カシオが製造するA159WAは、カシオファンにとっては垂涎の的だ。ただ残念ながら、日本で購入することは不可能である。
自動化ならば他社も行っているが、多品種に対応する点が大きな違いだ。山形カシオは製造ラインに柔軟性を持たせることで、自動化ラインで多品種製造を行うという、相反する課題を両立させたのである。
鍵を握るのが製造ラインの「モジュール化」である。具体的には、部品と、それを送るフィーダーがひとつのセットになっており、製造するムーブメントに応じて交換できる。
07年にこのシステムを完成させたカシオは、モジュールシステムを磨き上げることで、さまざまなムーブメントに製造ラインを合わせることに成功した。
加えて今や、一部のフィーダーも、カシオで設計するようになったとのこと。カシオのムーブメント製造ラインの製造数や種類を考えれば、かなりコンパクトにまとめられている。
加えて山形カシオは、自動化の一環としてIoTに取り組むようになった。まず同社が取り組んだのが、生産ラインの自動監視。続いては、そのデータを収集して、生産性の改善につなげるようになった。そういった試みのひとつが、20年に採用された故障感知システムである。
山形カシオは、パーツを供給する4台のスカラロボット(多軸ロボット)に集音マイクを取り付け、機械の不具合をチェックするようになった。これは骨伝導マイクを応用した技術であり、山形カシオ独自の技術とのこと。ロボットの振動が大きくなると、故障は近いと判断できる。結果として、製造ラインの維持は格段に楽になったそうだ。ロボットのメンテナンスは2年に1回のメーカー整備のみ、というからIoT化は、生産性を大きく改善したのである。
また、山形カシオは、モジュールに組み込むワッシャーの取り付けに画像処理を使うようになった。画像で位置決めをチェックするため、不具合は格段に減ったとのこと。もともと、製造ラインの自動化に取り組んでいた山形カシオは、生産ラインに即したIoTに取り組むことで、名実ともにマザー工場となったのである。
高級モデルの超絶ケーシング、PPLライン
そしてもうひとつの要素が、高級ラインだ。モジュールの製造ラインの奥には、さらに別に分けられてたPremium Production Line(PPL)が設けられている。ここで製造するのは、オシアナス、G-SHOCKの中でも高級版であるMR-GやMT-G、そしてプロトレックのマナスルなど。
10名の職人が、自動化ラインで製造されたモジュールを、手作業でケーシングしている。徹底した自動化を進める山形カシオにあって、この部門だけは例外だ。
オシアナス OCW-S7000を例に、ケーシングの工程を説明してくれた。
1.アナログモジュールに、基板やソーラーセルを固定する。
2.文字盤を固定する。
3.小さな針を固定する。
4.時分針などを取り付ける。
5.針の水平をチェックする。
6.針位置を再チェックする。水平ではなく、複数の方向から確認する。
7.すべての針をチェックする。
8.拡大鏡を使ってモジュールをケーシングする。
9.ホコリをチェックする。
10.温度テストをする。
11.裏蓋を圧入する。
12.機械による針ズレのチェック。
13.防水テストをする。
14.時計とバンドを脱磁する。
ちなみにオシアナスの品質チェックは、MR-G相当とのこと。つまりカシオの中で最も厳格というわけだ。
職人がケーシングを行う理由には納得させられた。針を正しく取り付けても、文字盤の印字などによって、ずれて取り付けられているように見える場合がある、という。つまり、人間の目に正しく見えるよう、細かく針位置を確認するわけだ。
なるほど、PPLの工程が、機械ではなく人に頼るのは納得だ。ある職人はこう語った。「針の位置を正しくみるには、目が悪いとダメなのです。ですから、暗い場所でスマートフォンは見ないようにしていますよ」。
まだまだ見所はいっぱいある
今回の訪問では、山形カシオの肝と言うべき微細な金型技術をみることは出来なかった。しかし、組み立てを見るだけでも、山形カシオの工場は、いわゆる時計工場のレベルを超えた、スーパーファクトリーであることが分かる。
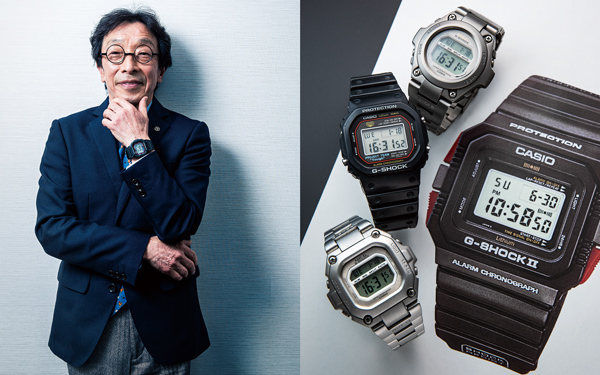
https://www.webchronos.net/features/91803/
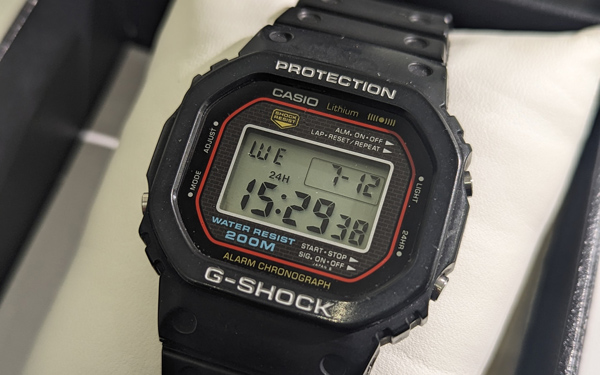
https://www.webchronos.net/news/99334/
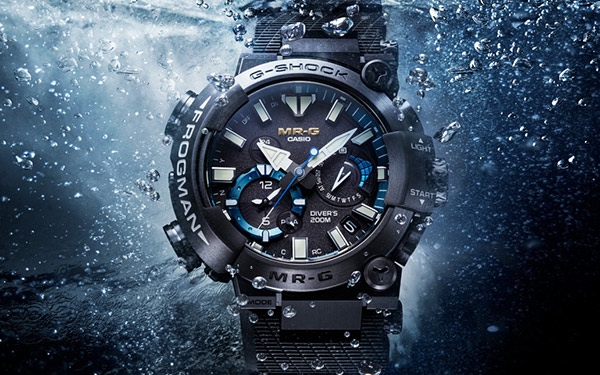
https://www.webchronos.net/features/93522/