HIGH-TECH CERAMIC(ハイテクセラミックス)
ラドーのハイテクセラミックスを手掛けるのは、スウォッチ グループ傘下のコマデュールである。セラミックスを腕時計の外装に採用する時計メーカーが増えたとはいえ、実際にセラミックスを自製できるメーカーは非常に稀な存在だ。その筆頭が、グループ内にコマデュールを擁するハイテクセラミックスの先駆者、ラドーである。
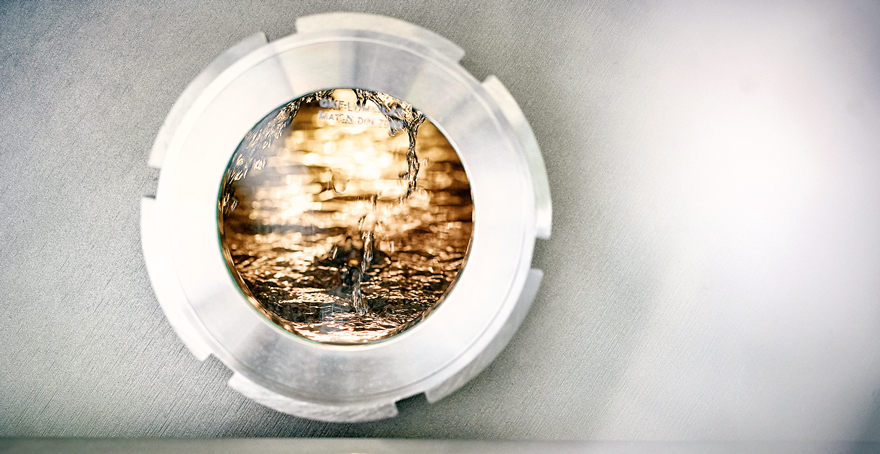
ハイテクセラミックスの原料である酸化ジルコニウムと顔料、つなぎのポリマーバインダーの粉末を高温で溶解し、射出成型したモールドを焼結する前に、バインダーをモールドから取り除くデバインディングの工程。アルコール溶剤で満たしたオーブンに入れ、60℃で2時間処理することで、プラスティックをアルコールで溶かし、バインダーを除去する。
(右)ハイテクセラミックスの原料である酸化ジルコニウムの粉末。この粉末に色を付ける顔料と、つなぎとなるポリマーバインダーを混ぜて、高温で溶解後、約170℃の状態にして1000気圧で複合鋳型に射出成型する。(中)バインディングとなるポリマーバインダーのペレットの上に置かれたプラズマハイテクセラミックス製のブレスレットリンク。(左)成型されたパーツを焼結する前にデバインディングしている様子。デバインディング工程では、寸法を変えることなく、ポリマーバインダーのみをアルコール溶剤で溶かして除去するため、モールドは多孔質になる。
ラドーのハイテクセラミックスは、高純度の酸化ジルコニウムの粉末を原料として成型・焼結させて製造される。ただし、酸化ジルコニウムの粉末だけでは固まらないため、つなぎが必要だ。その役割を果たすのが、成形助剤のポリマーバインダーである。さらに顔料を加え、型を用いて成型するのだが、ラドーでは2011年以降、この作業をインジェクションで行う。原料を顔料、バインダーとともにオープン型に圧入して成型する手法に対し、ラドーでは高温でこれらの原料を溶解し、複合鋳型に約1000気圧で射出して成型するのだ。これこそ同社が長年にわたって蓄積してきたノウハウの結晶と言っても過言ではない。
最も驚かされたのが、この複合鋳型には歯車を組み込むことができ、可動式になっていることだ。この仕掛けにより、射出成型の際、同時にバネ棒用の穴をラグに開けることができる。穴を開けた後、可動部を穴から抜き取ることができるからだ。オープン型ではこうした3次元的な加工はできない。
インジェクションによって、セラモスのケースを射出成型している様子。複合鋳型に溶かしたバインダーと酸化ジルコニウムを射出する際には、精密な型の隅々にまで原料を行きわたらせなければならない。そのための液体の最適な温度が約170℃である。写真は、セラモスを射出成型後にパーツを取り出すところ。左側に見えるのが精密な複合鋳型である。
(右)複合鋳型に組み込まれた可動部の歯車。この歯車が型の内部の可動パーツを動かして、ケースサイドのリュウズやプッシュボタンの穴、ラグのバネ棒の穴、ブレスレットリンクの穴などを開ける。(中)インジェクションによって成型されたハイテクセラミックスのパーツは、ひとつひとつロボットアームで型から取り出され、ベルトコンベヤーで次の工程に運ばれる。(左)オーブンでパーツを焼結する様子。450℃で2日間ほど焼結されると、パーツの重さは変わらないが、体積は約23%縮む。この収縮率を考慮して、複合鋳型の寸法は精密に設計されている。
(右)プラズマハイテクセラミックス加工の様子。焼結されたホワイトセラミックスのパーツを研磨した後、特殊な炉の中で約2万℃のプラズマによって活性化された水素とメタンガスにさらす。すると、まるで金属のような輝きを持つ独特な外観を帯びる。(中)プラズマ処理中のパーツ。2万℃のプラズマによって、表層部の酸化ジルコニウムの酸素原子が炭素原子に置き換えられ、炭化ジルコニウムとなることで、メタリックな光沢を放つようになる。(左)プラズマ処理された後のケース。表層は金属のような質感を得るが、素材はハイテクセラミックスのままである。
CERAMOS
創業以来、ラドーが追求する「傷つかない」「美しい外観が永遠に続く」素材。ハードメタルに次いで、同社が白羽の矢を立てたのが、“新素材”として時計業界に導入されたハイテクセラミックスである。皮肉にも、身近な素材になってしまったが故に、今では、その真の価値が分かりにくくなってしまったことも否めない。ラドーは、その色や形に革新をもたらすことで、今なお“新素材”としてのハイテクセラミックスの可能性を切り開き続けている。
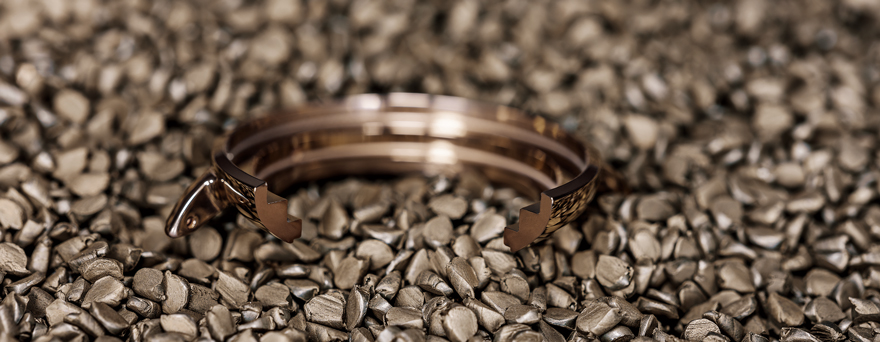
表層部の組成を変えることで、金属のような光沢を放つプラズマハイテクセラミックスに対して、90%のハイテクセラミックスと10%の合金で構成されるセラモスは、焼結の過程で金属部が融解してセラミックスの組織と再結合するため、金属のような組成を再生成する。写真のケースの断面を見れば一目瞭然。内部まで組成が同じため、素材の色は一様だ。
セラモスとは、ハイテクセラミックスに約10%の金属の合金を混ぜて焼結したサーメットと呼ばれる素材の一種である。セラミックスの特性である硬さを維持したまま、金属のような光沢と質感を与えることができる。結果、一般的なセラミックスとは大きく異なる外観をかなえ、個性を際立たせてきた。だが、ここでひとつの疑問が湧き上がる。セラミックスに金属のような質感をもたらす技術として、プラズマハイテクセラミックスを持つラドーが、なぜセラモスという技術を必要としたのだろうか?
実は、このふたつの技術は、ケース表面の仕上がりはよく似ているが、その加工工程はまったく異なる。後者は、金属のような外観に反し、実際は金属を含まない純粋なセラミックスである。対して、セラモスは10%ほど金属合金を含む。この点にこそ、ラドーのラドーたる所以が見て取れる。すなわち、セラミックスに金属の質感を求めるとき、決してひとつのやり方で満足せず、多様なソリューションを模索する。しかも、さらなる完璧さを追求し続ける。同社の研究開発部はこう明言する。「セラモスのほうが、よりステンレススティールカラーに近い」。
そもそも、ラドーが1986年に採用したハイテクセラミックスは黒しかなかった。91年には白が可能になり、98年にプラズマを用いて金属を使用せずに金属のような質感を実現した。金属でも有機物でもないセラミックスに色の多様性とさらなる付加価値を与える挑戦。ここにこそ、ラドーの哲学であるイノベーションが最も象徴されている。その最新成果が、完璧さの追求に約10年を要したローズゴールドカラーのセラモスなのだ。
(右)ハイテクセラミックスに10%の金属合金を混ぜて焼結したセラモスは精密なモノブロック構造を持つため、最小限の切削で済むが、セラモスのために開発された専用工具を用いて、専用のプロセスで切削するため、ハイテクセラミックスに比べて長い時間を要する。(中)焼結した直後はマットな状態のケースのバリを取って均し、表面を研磨することで、金属のような光沢を発するようになる。セラモスはハイテクセラミックスに比べて硬いため、専用の工具を用いてバリを取るのに5~10倍の時間を要する。(左)こうして仕上げられたケースは見事な輝きを放つ。