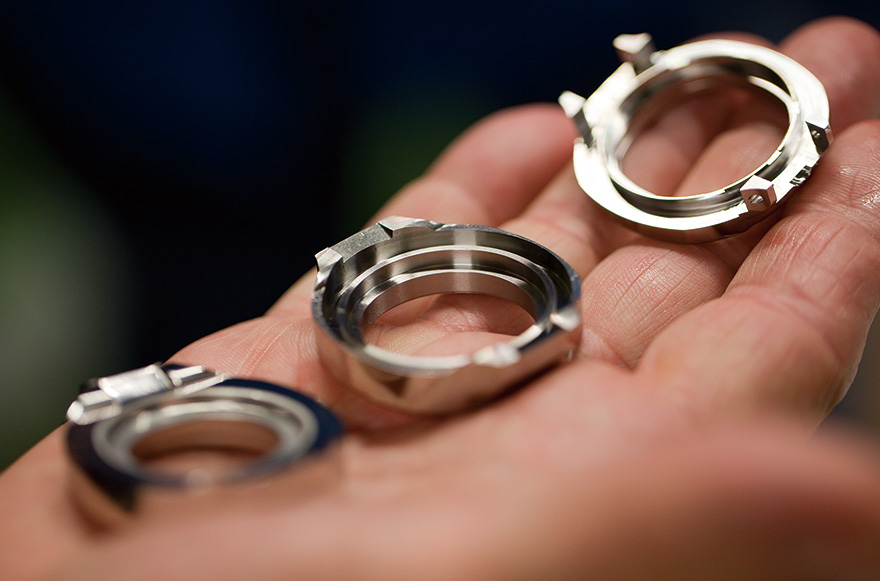
古典と最新鋭の製造ノウハウが交差する場所
ジュネーブ郊外の工業地域、プラン・レ・ワットの本社工場のすぐ近くに、その工房はあった。前身のサプライヤーからパテック フィリップの傘下に入って熟成を重ねた今、ほぼすべてのラインナップのケースとブレスレットを作る外装製造の拠点にまで成長した。
ノーチラスのケースもここで作られる。優れた外装の加工精度を誇る希代の“スポーツウォッチ”が生まれる瞬間に立ち会った。
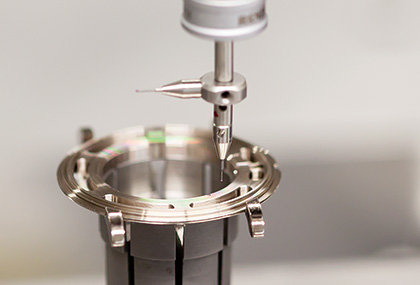

ノーチラスのオリジンを決定づける肝は何か? いうまでもなくケースの造形である。ガスケットを挟んでベゼルを胴に密着させ、さらにベゼル両サイドの「耳」からネジ留めする特殊な構造が、高い機密性とアイコニックピースにふさわしいルックスの両方を与えているのだ。現行ノーチラスの製法の奥義を知りたければ、ケースの製造現場へ出向けばよい。そんな帰結を強引に導き出し、ジュネーブ郊外、プラン・レ・ワットにあるパテック フィリップ本社工場からわずか数キロの至近距離にあるケース及びブレスレット製造工場を訪れた。訪問当日は、ノーチラスの製造ラインが稼動しているという嬉しい報告も入った。
ペルリーという町にあるこの工場には、初訪問ながらちょっとした思い入れがある。1995年にパテック フィリップの本社(当時はローヌ通り沿いにあるブティック上階に製造設備があった)を初取材した後、プランパレ広場至近のアトリエ・レユニというケース・ブレスレット工場を訪れた。数百人規模の工員が働く比較的大きな工場は、パテック フィリップの重要なサプライヤーだ。ここで若き日のティエリー・スターン氏が時計製造のノウハウを学んだという逸話も残る。96年にパテック フィリップはこの工場を買収した後、同年プラン・レ・ワットに完成なった新社屋にケース・ブレスレット製造部門として収めた。パテック フィリップの従業員数が900名を超えた2003年、旧アトリエ・レユニは多くの工作機械などの製造設備と従業員を収めるのにうってつけの、フロア面積5000㎡に及ぶ現在の建物へ移転したのだ。ちなみに、プランパレ広場近くの旧社屋は、パテック フィリップ・ミュージアムへと生まれ変わった。
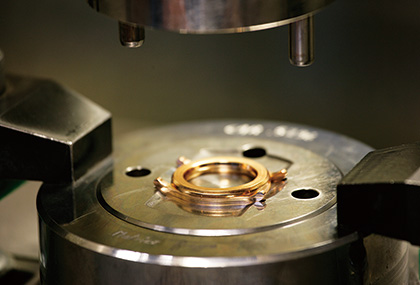
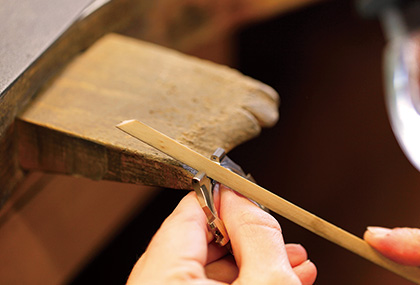
ファクトリービジットに入ろう。今回の案内役はダニエル・ジャケ氏。パテック フィリップ創業125周年に当たる1964年3月15日に入社した彼は、ムーブメントのパーツ製造全般を統括する役職などを経て、2006年に退職。現在は嘱託でテクニカルな工場見学のガイドやバーゼルワールドにおける新作のプレゼンテーションなどを行っている。
最初に訪れたのはプレス部門だ。帯状の素材からカットされた塊は、冷間鍛造プレスによって成形されていく。「ゴールドやプラチナはもちろん、ノーチラスに用いられるSSケースも冷間鍛造が用いられます。1回プレスするたびに炉に入れて加熱し、分子構造が戻って柔らかくなるので繰り返し行う次のプレスが容易になります。この工程は、少なくとも10以上、20工程に及ぶこともあります」。プレスはもちろんCNCで行われるが、この工房の片隅には、2mに達しようかという巨大な手動プレス機がある。旧式の冷間鍛造プレス機だそうで、現役を退いたこの工房のシンボル的な存在ながら、今でもまれに、ブレスのコマの浮き彫りなどの表面装飾に使われることがあるという。
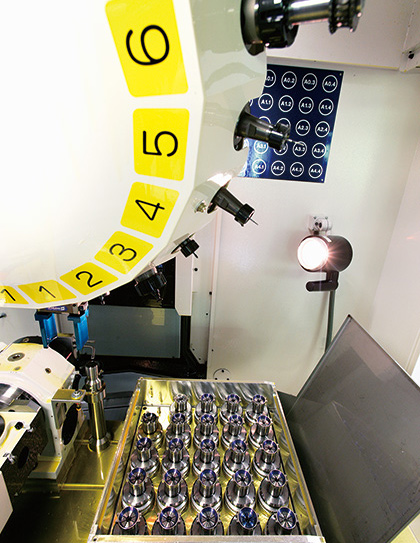
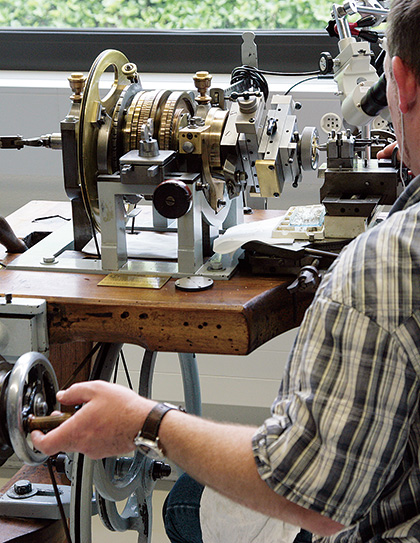
プレス加工、旋盤(切削)加工、フライス加工と順を追ってケースのエレメントは徐々に形を成していく。各工程が終わるたびに、3次元測定器による寸法検査が行われる。
「切削機械のツールがもし磨耗していたら、設計図面の寸法どおりには仕上がりませんのでね。許容誤差は5から10ミクロンです」
地階ながら外光がたっぷり注ぐ快適な工房内を鵜の目鷹の目で徘徊していくと、思いがけない光景に出くわす。20世紀初頭製とおぼしき手動のギョーシェ旋盤を使って職人が文字盤にギョーシェ装飾を施している。クロノメトロ・ゴンドーロの文字盤であることは一目瞭然だ。何故、ケースを作る工場内で文字盤の特殊加工が行われているのか。
「このマシンは1905年製です。もともとパテック フィリップが所有していたのですが、協力工場である文字盤メーカーのフルッキガー社が手動旋盤によるギョーシェの技術を保持していなかったために、旋盤を貸し与えたのです。協力工場、そして今は我が社の傘下にあるフルッキガーに十分ノウハウが蓄積されたので、こちらに戻してもらったのです。彼(職人)はフルッキガー出身です」
パテック フィリップの技術を蓄積するための、つまり未来に向けた投資はこんな小さなところにまで及んでいるのだ。
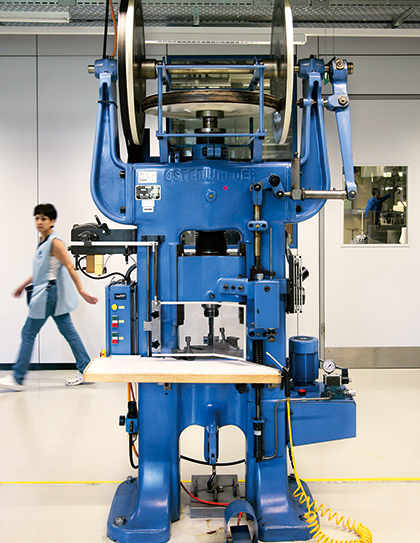
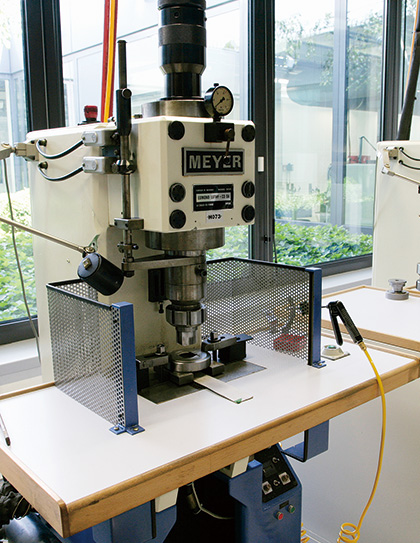
パテック フィリップの技術を蓄積するための、つまり未来に向けた投資はこんな小さなところにまで及んでいるのだ。
「次はポリッシュの部門をご案内しましょう。ノーチラスの、とりわけベゼルはサテン、ポリッシュ、サンドブラスト仕上げが複雑に組み合わされているので、工程は17から20にも及びます」
ここには30名のポリッシャーが配属され、ノーチラス専任は6名。ベゼル、胴、ケースバックはすべてここで仕上げられる。外観について規準のないジュネーブ・シールから離脱し、独自規準のパテック フィリップ・シールを導入して以降、美観に関する要求値はさらに高まったとポリッシャーたちは口を揃える。「いうなればゼロディフェクト。欠陥は絶対に許されないのです。ケースの寸法精度もますます厳しくなりました」。
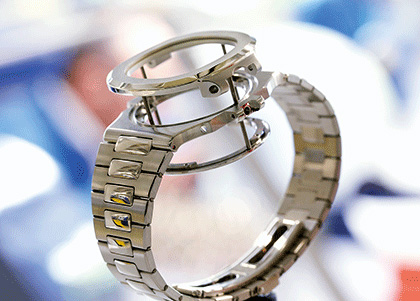
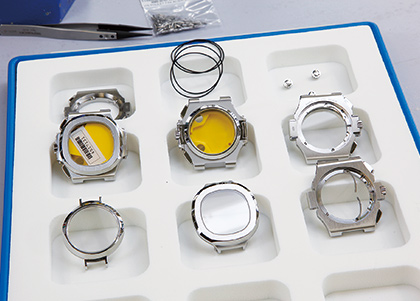
スイスにはポリッシャーの連邦資格があるというが、仮にこの連邦資格を有していて、他メーカーで15年近くのキャリアを有している〝ベテランの〟ポリッシャーでも、パテック フィリップに雇用された場合は、最低でも1年間のトレーニングを積む必要があるという。
「私は他のメーカーのことはよく知りません。でも、そうしないと、彼らはパテック フィリップの求めるクォリティに見合った仕事ができないんですよ」
最後にケースの組み立て部門を訪ねた。12名の組み立て工のもとに届けられたノーチラス(Ref.5980/1A)のパーツは、完全なフィニッシングが施されている。彼らはそれに加圧・減圧テストを施し、そののちに手作業での機能検査(プッシュボタンやコレクトボタン)を加え、合格後にそれらのパーツを組み上げて完成品とする。完成品の内部にはムーブメントを模したプラスティックのダミーを入れて仮の防水検査が行われる。
ここには1500人の従業員が働き、最新のCNC工作機械もあれば、旧式の工作機械も大事に保存されている。すべて、古典も最先端も含めたあらゆる技能を蓄積したい。その目的のためだけの措置。だから、この工場はほぼすべての製品のケースを製造している。もちろん、数量からすればサプライヤーの協力を仰ぐ必要はあるだろうが。「製造の拠点はここでなければならない」と最後に力強く語ったダニエル・ジャケ氏の言葉がいつまでも耳の奥に残った。
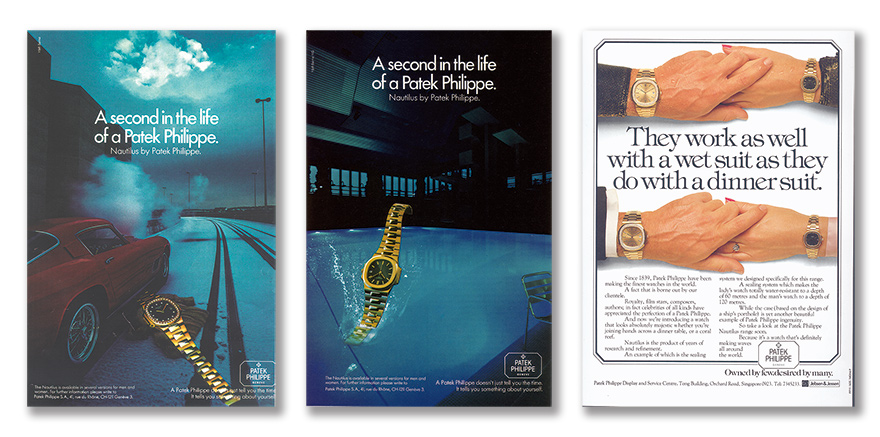