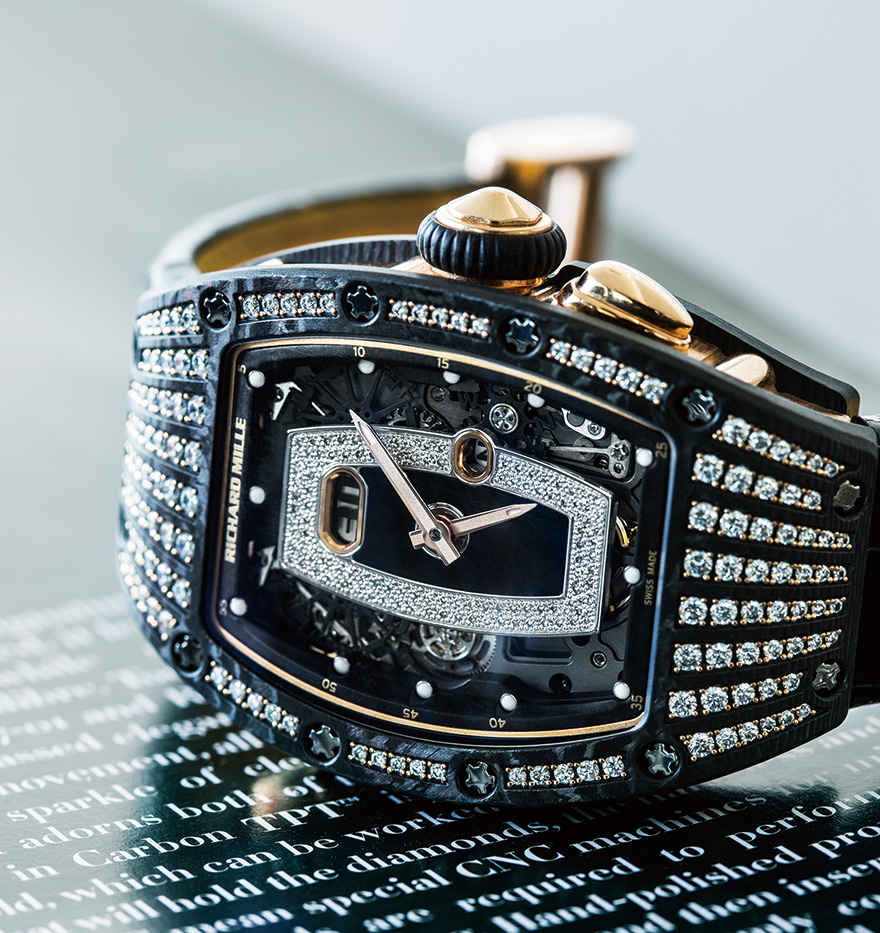
カーボンTPT™にパヴェダイヤモンドをセットしたモデル。プロアートが行うのはケースの製造と、下地の整面のみ。セット自体はラ・ショー・ド・フォンの会社が行っている。しかし歪みのないセッティングは、完全に歪みのないケースがあればこそ。予価1840万円。
スイスのケースメーカーがこぞって採用する切削プロセス。しかし話を聞くに、同社の在り方は他メーカーとまったく異なっている。求められるオーダーはミクロン単位と複雑時計のムーブメント水準なのだ。そんな同社が、今やケースだけでなく、ムーブメント部品も作るようになったのは当然だろう。複雑時計の基準でケースを作る工房、プロアート。その高精度を支える要素は大きくふたつある。最新の工作機械と、独自のノウハウだ。
工房に足を踏み入れると、至る所に最新の工作機械が並んでいる(社名は企業秘密につき明らかにできない)。バラン氏曰く「機械はすべて1年から5年前に購入したもののみ」とのこと。しかもフルーリー製の「モデューロ」のような生産性を重視したものではなく、スイスやドイツの工作機械でも、高精度を誇るものばかりだ。筆者はさまざまなケース工房を訪問したが、掛け値なしに、プロアートの設備は突出している。複雑時計の工房でも、これほど揃えたところは希ではないか。「工作機械は15台ある。価格は一台35万〜55万スイスフラン。かなり投資していると思う」(バラン氏)。
ケースの製法に何の秘密もない。角材から荒削りでケースの形を出し、切削を加えて形を整えていく。立体的な側面は、切削ではなく、カーボンシリシウムのディスクを使った研削によるものだ。研ぎながら削っていく研削は他社もケース作りに用いている。普通は研削の後に研磨を施して最終的な完成形にするが、プロアートは、基本的に研削だけで側面を完成させる。かなり乱暴に思えるが、加工に自信があればこそだろう。
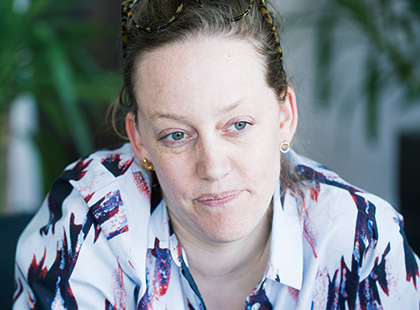
「RM 67-01」のベゼルを見せてくれた。以前はスタンピングで型を抜いていたが、残留応力が残るため、切削に改めたとのこと。丸い棒材の外と中を削り、2枚のベゼルに成形するのである。切削に要する時間は、表と裏で1時間半。求められる加工精度は1ミクロンから4ミクロンというから、ミニッツリピーターやグランソヌリのムーブメントと同基準と考えていい。ちなみに同社は放電加工機を使ってローターの穴抜き加工も行っているが、その精度も7ミクロンと、ムーブメントの軸穴以上だ。
もちろん、最新の工作機械でなければ、そもそもここまでの精度は出せない。しかし加工のノウハウが伴わなければ、10ミクロンの壁を超えるのは極めて難しい。ではそのノウハウとは何なのか。現在の工作機械(とりわけドイツとスイスの機械)は、精度を出すよりも、生産性を上げる方向で進化している。モデューロのように、部材を投入してボタンを押せば勝手に加工してくれる機械が一例だろう。しかしプロアートの工房では、生産性は課題にさえ入っていない。「少量生産だから高品質を維持できる」とはどの会社も使いたがる売り文句だが、同社の作業現場を見れば、掛け値なしに事実と理解できる。設備を見た限りで言うと、同社は年に最低10万個のケースを作れるだろう。しかし2016年の実績によると、生産数はわずか3500個にすぎない。