エンジニアリング〟の転換点
高耐磁時計からマルチマテリアルの拡充へ
パイロット・ウォッチから派生を遂げて、高耐磁性能を備えたコンシューマーモデルとして進化してきたインヂュニア。しかし2013年の大刷新では、“脱・耐磁時計”とも呼ぶべき、新たな方向性を打ち出してきた。ここではその試みのひとつである、ケース加工の発展と新素材導入にフォーカスする。
Ceramics
酸化ジルコニウム基のブラック・セラミックスケースを採用。ベゼル表面のみをポリッシュで仕上げるなど、表情に変化を付けている。ベゼルを留めるビスはチタン製だが、ヘッド部分のみセラミックス製。自動巻き(Cal.80110)。28石。2万8800振動/時。パワーリザーブ約44時間。直径46mm。122万5000円。
Titanium
1980年代から自製に着手していたチタンケースを持つモデル。ベゼルやラグはサテンで仕上げるが、ケースサイドには同社チタンケースらしい、サンドブラスト加工を残す。24時間針はセンター配置。自動巻き(Cal.35720)。27石。2万8800振動/時。パワーリザーブ約42時間。直径45mm。71万円。
Titanium aluminide
超硬合金に代わる素材として研究が進む、チタンアルミナイドをケースに採用。難切削材の筆頭だが、美しいサテン仕上げを誇る。プレスよりも切削工程により重点を置く、IWCらしいケース加工だ。自動巻き(Cal.89802)。51石。2万8800振動/時。パワーリザーブ約68時間。直径46mm。499万5000円。
脱・耐磁時計。2013年の大刷新に伴い、インヂュニアはより一般的なスポーツウォッチとしての性格を強めた。今や高耐磁性能は、スポーツウォッチが標準装備して然るべき〝必須スペック〟となりつつある反面で、常識を越えた「超耐磁性」も(機械式時計の扱いを心得ているならば)不要となりつつある。そうした意味で、新しい「インヂュニア・オートマティック」に盛り込まれた4万A/mという耐磁性能は、適度な〝落としどころ〟であったろう。では、ニューコレクションは「インヂュニア=エンジニア」たる矜持をどこに表現するのか? そのひとつの回答は、従来さまざまなモデルに盛り込まれてきた、複雑機構と素材的な試みを集約することであった。特にケース素材に関する試みは、かつてのIWCが先駆者となった分野のひとつである。
1980年代以降、IWCはケースの内製化に着手するが、その契機となったのはチタンケースだった。80年にIWCは、純チタンケースを備えた「チタニウム・クロノグラフ」(ポルシェデザイン銘)を製造開始。軍用の「オーシャン2000」では2%のアルミニウムを添加した合金チタン(グレード5)を用いた。当時、チタン切削を行えるケースサプライヤーがほとんどなかったという背景が、IWCのケース内製化のきっかけとなった点は興味深い。ノイハウゼンにケース工場が完成し、大部分を自製できるようになった現在でも、同社はプレス加工よりも切削加工に重点を置く。これは硬いセラミックスでも同様で、驚くべきことに同社は、円柱に近い形状に焼成されたセラミックス素材から、ケース形状を削り出しているのである。
IWC初のカーボンケースを用いた限定品。詳細な製法は不明だが、外観から判別できる範囲では以下の通り。ダイアル、ベゼル、ケース表面(アウターケース、ケースリング)がカーボンシートをプレスした後に焼成加工。バックケースがチタンリング+カーボンシートの高温高圧プレス。ケース裏に不均一なカーボン繊維の切削跡が見られるが、この点は情報が得られなかった。またカーボン繊維は紫外線に弱いため、ケース表面に施されるトップコートには、UVカットの意味もあるはずだ。自動巻き(Cal.80110)。28石。2万8800振動/時。パワーリザーブ約44時間。直径46mm。212万5000円。
粉末冶金による焼成材料からの切削という点では、チタン加工とセラミックス加工には共通点があった。この延長線上に位置するのが、2013年のコレクションに投入されたチタンアルミナイドである。素材の名称から、単純にチタンとアルミの合金だと思われがちだが、それではこの素材の凄みは伝わらない(それだけではグレード5チタンと同じ)。〝アルミナイド〟と呼ばれる金属間化合物の組成技術は、いわゆる〝超硬合金〟に代わる素材として研究が進められているもので、資源偏在性の高いタングステンや、価格変動の激しいコバルトなどのレアメタルを結合相に用いず、同等以上の特性を付与しようという試みである。その究極は、研究過程にある鉄アルミナイドだ(「シンセシオロジー」2010年VOL.3/№4より要約)。アルミナイド化された金属に求められる要点は、工具や金型に使用できる硬さ(チタンアルミナイドの場合は約1000Hv)と、高速切削や無潤滑切削を可能にする逆温度依存性(=耐熱性)である。現在では硬さと耐熱性、そして粉末冶金の基本特性でもある、比重に対して軽量に仕上がる(=密度は低い)という利点を活かし、レーシングマシンのバルブや、ジェットエンジンのタービンに使用例が見られる程度だ。
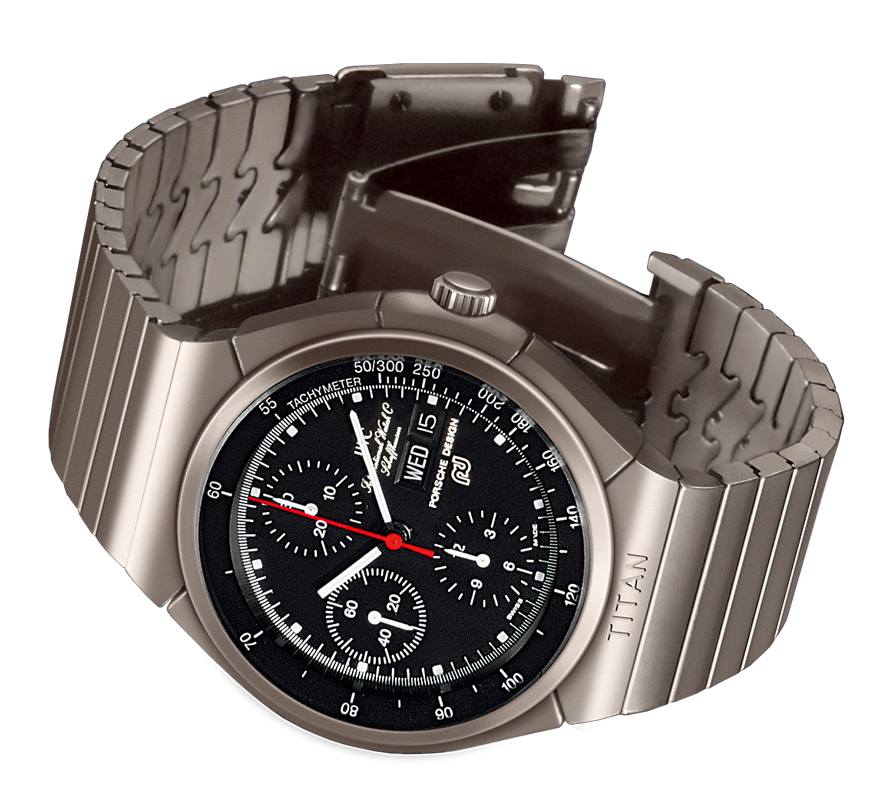
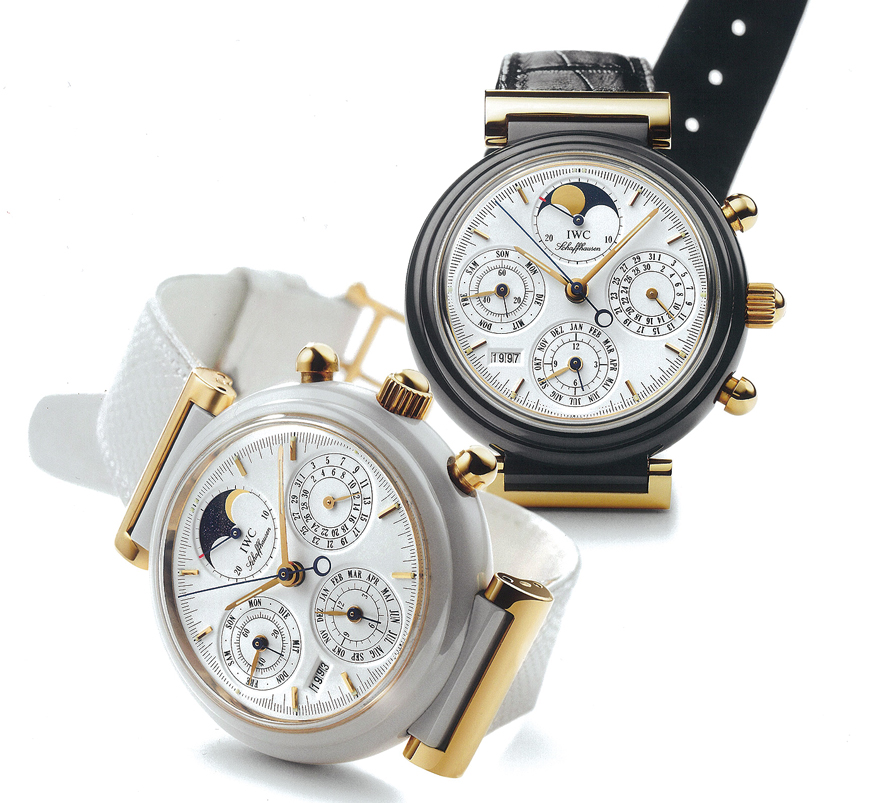
もうひとつの試みはカーボンケースである。ただし、従来の〝フォージドカーボン〟(カーボン繊維を高圧、高温焼成してケース形状に成形)とは異なり、カーボン繊維を均等に織り込んだシートを素材に用いている。プリプレグされた(=熱硬化性のエポキシ樹脂を予め染みこませた)カーボンシートを型に張り込んで焼成している点は明確だが、その中身については、現時点では情報が錯綜気味だ。製造現場に近い部門からは、シートのミルフィーユ(積層)や、カーボン繊維を含む樹脂の注入という声も上がり、一方でデザイナーのクリスチャン・クヌープは、芯材へのカーボンシートの張り込みだとコメントした。筆者はどれかひとつが正解という訳ではなく、すべての組み合わせだと踏んでいるが、正確な情報は追ってお伝えすることにしたい。