創業間もなく、マニュファクチュール化に取り組んだフランク ミュラー。完成を見たのは実に2019年のことだった。時間がかかった理由は、できうる限りを内製化しようとしたため。スイスに自社一貫生産を謳うメーカーは少なくないが、内外装の設計から、ムーブメント部品の製造、そして組み立てから最終検査までウォッチランドに集約したフランク ミュラーのようなメーカーは決して多くはない。
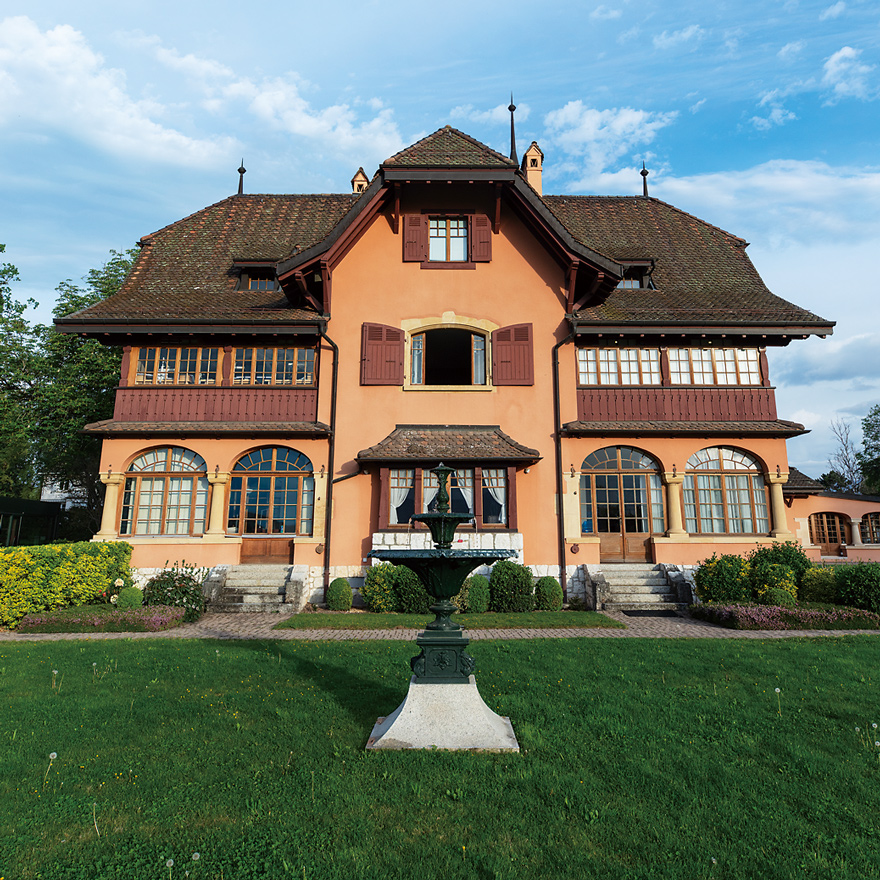
広田雅将(本誌):取材・文 Text by Masayuki Hirota (Chronos-Japan),
Edited by Yukiya Suzuki (Chronos-Japan)
[クロノス日本版 2024年9月号掲載記事]
ウォッチランド
「マスター オブ コンプリケーション」の証明
R&D部門のプロトタイピストとして「エテルニタス」などの開発に携わったパスカル・オッフォアは語る。「フランク ミュラーという会社は時計業界の中でも異例の道をたどってきました。ウォッチランドの中で全部できてしまうから、自由度が高いのです。ゴレイ氏のおかげですね」。彼が述べた通り、フランク ミュラーのマニュファクチュール化は大設計者ピエール・ミッシェル・ゴレイの下で大きく進んだ。彼は2000年代初頭からウォッチランドの内製化を推し進めたのである。
同じくR&D部門のパトリック・ペレも補足した。「それ以前のフランク ミュラーは、ベースムーブメントと独自のモジュールの開発環境が違っていた。だから、できるだけ自社製にしようと思ったのです。入社した2006年には『フライングT』も『レボリューション3』も『ミニッツリピーター』も、小さなトゥールビヨンもありましたよ」。
時間をかけてマニュファクチュールに成長したフランク ミュラーには、結果として多くのノウハウが育った。オッフォアが明かしたのは、「エテルニタス・メガ」に関するエピソードだ。
「エテルニタスのクロノグラフを組み立てる際に、普通の加工精度だと遊びが取れないのです。放電加工機で部品を作っても、100分の5mm以下の厚みの部品は作れないと断られた。そこで私が手作業で10ミクロンだけ削りましたよ」
彼は事もなげに言うが、どれほど優れた職人でも、手作業で100分の1mmを削るのは極めて難しい。しかしこういった「マスター」たちは、ウォッチランドの至る所にいる。
すべてをウォッチランドの下に取り揃える、そして、できる限りを内製化するというフランク ミュラーの在り方は、組み立て部門にも良い影響をもたらした。説明してくれたのは、トゥールビヨン工房の責任者であるダミアン・デストだ。
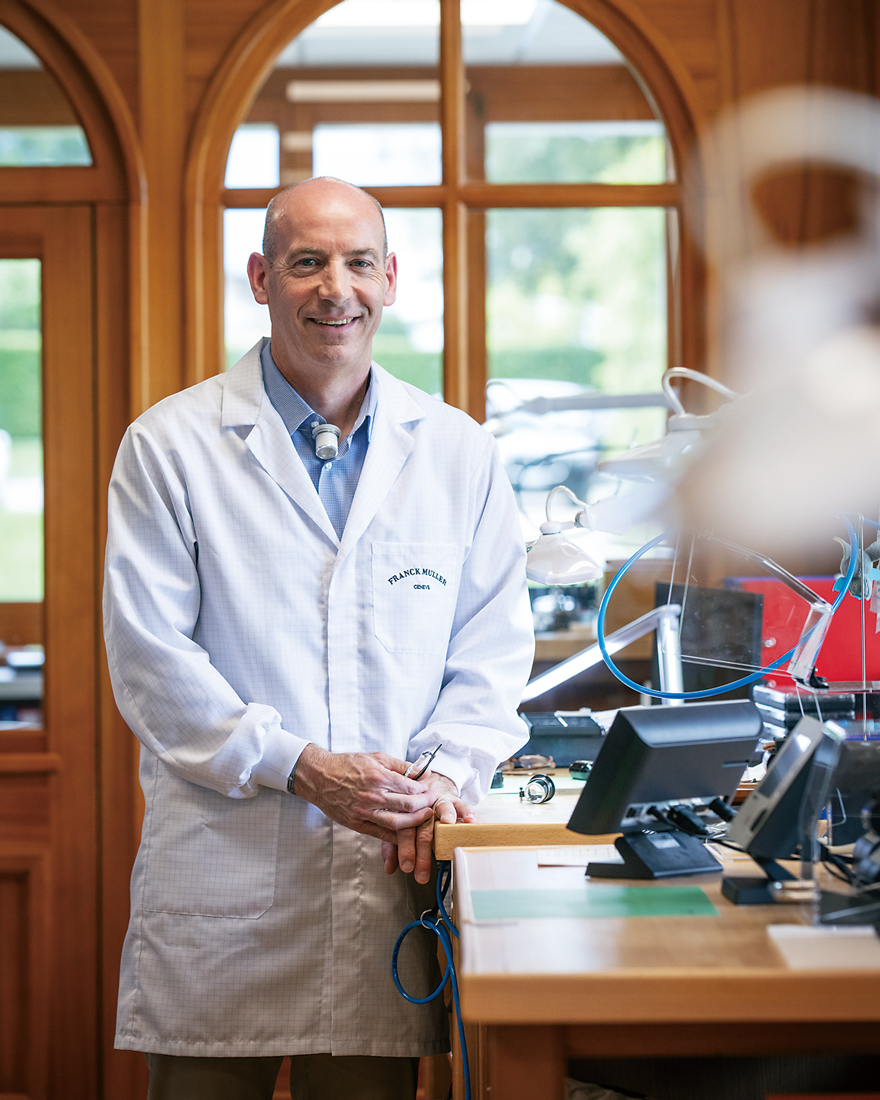
「正直、問題は昔と同じぐらいありますが、前より早く解決できるようになりましたね。設計と製造が、みんな同じ場所にいるからです」
彼が例に挙げたのは、直径16.70mmのテンワを持つ「ギガ トゥールビヨン」だ。
「最初に作ったギガ トゥールビヨンは、キャリッジが大きすぎてショックに耐えられないことに気づきました。すぐに設計部門に連絡を取ったところ、衝撃が加わった際に、ホゾが石から離れないようなロック機構が加えられたのです」
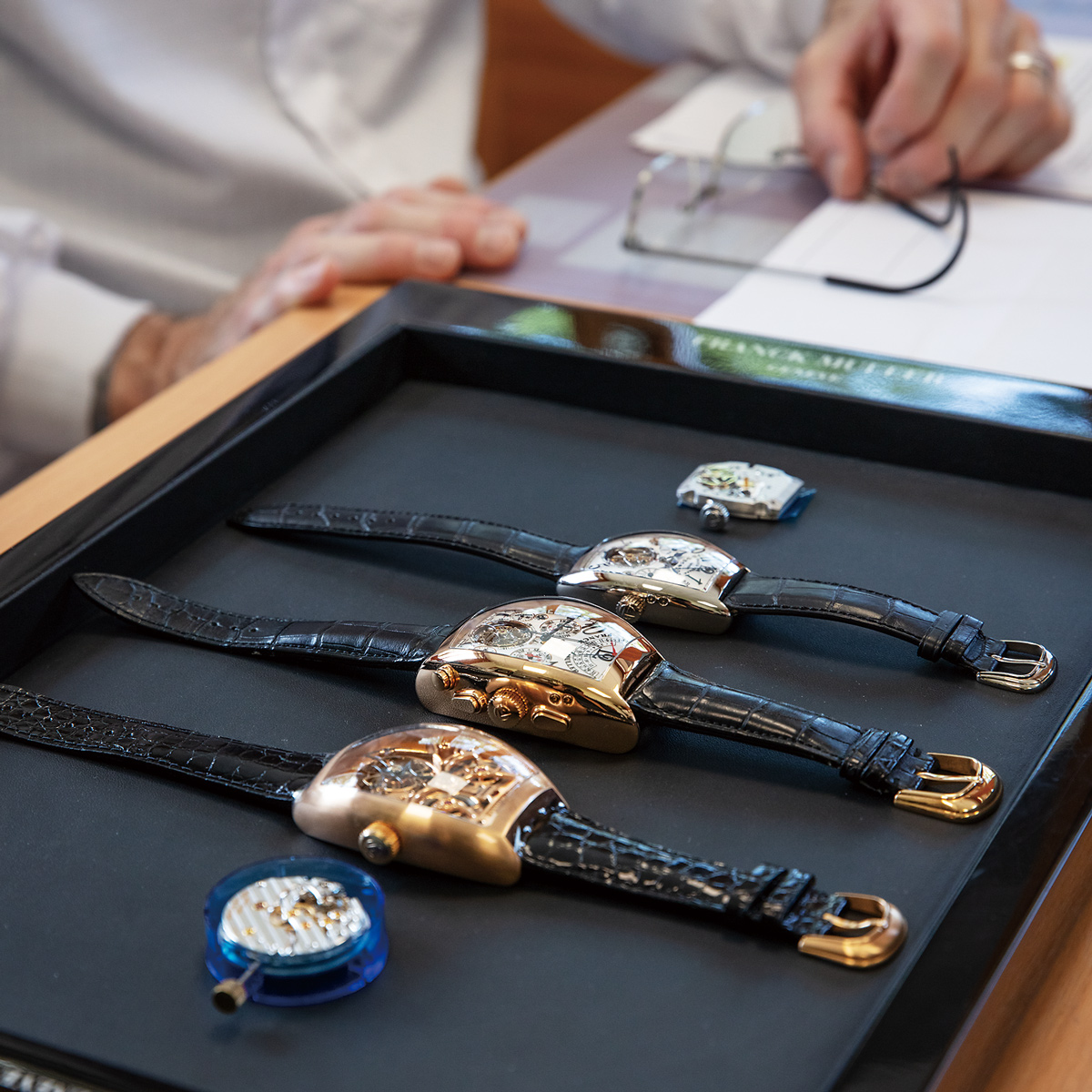
トゥールビヨンを組み立てる工房内では、なんと香箱が組み立てられていた。普通は主ゼンマイを収めた状態で購入するが、ウォッチランドでは納品された主ゼンマイを自社製の香箱に組み付け、全数のトルクを計算している。担当者曰く「あえて社内で組み立てているのは、トルクが違っていたらすぐ交換できるから」。
近年フランク ミュラーは、手巻きムーブメントとしては珍しく、スリップする主ゼンマイを採用するようになった。不具合が生じにくいがトルクの管理は難しい。トルクを全数検査するフランク ミュラーだからこその試みだろう。ほかにも香箱の組み立てだけではなく、コハゼやアンクルへの爪の取り付けといった、他社ではサブアッセンブリー部門に委ねられる作業が行われていた。
取材時に組み立てられていたのは、23年に発表された「グランド カーベックス ギガ トゥールビヨン」である。「テンワが大きいから時計師たちにとっては難しいムーブメントではない」とデストは語るが、それはエテルニタスなどと比べての話だ。ギガ トゥールビヨンのテンワの慣性モーメントは、11年のオリジナルでも64.4㎎・㎠、最新版では69.4㎎・㎠もある。それを軽いチタン製とはいえ、直径20mmのキャリッジに収めるのだ。片重りを取るのも、軸に歪みを出さないのも決して容易ではない。
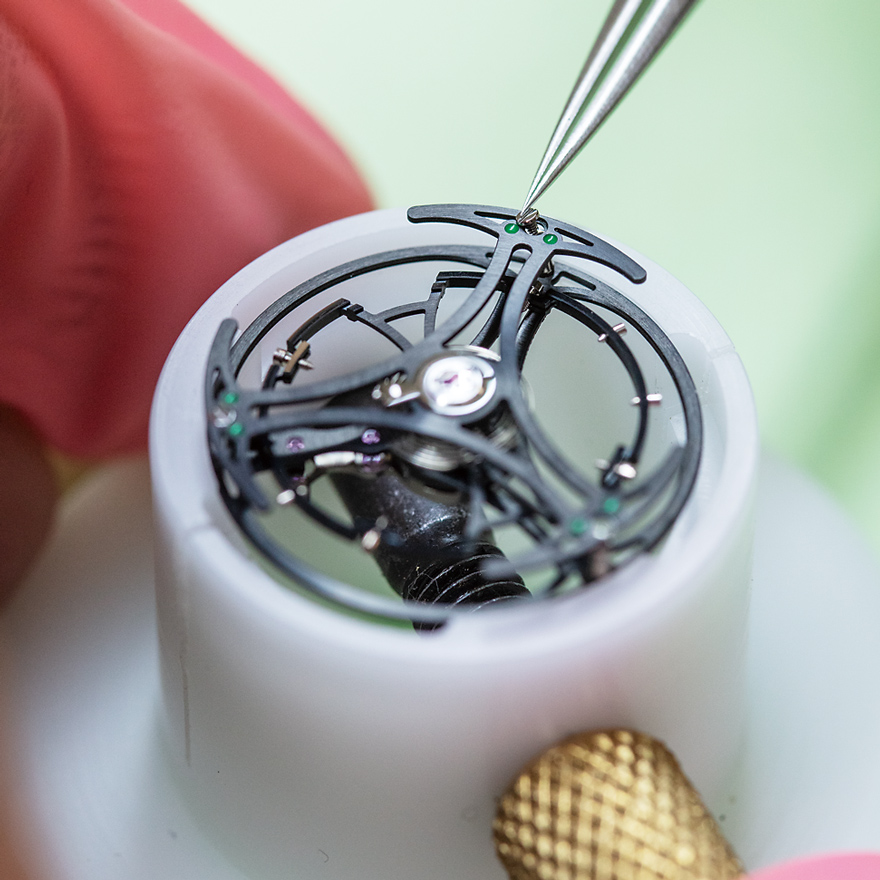
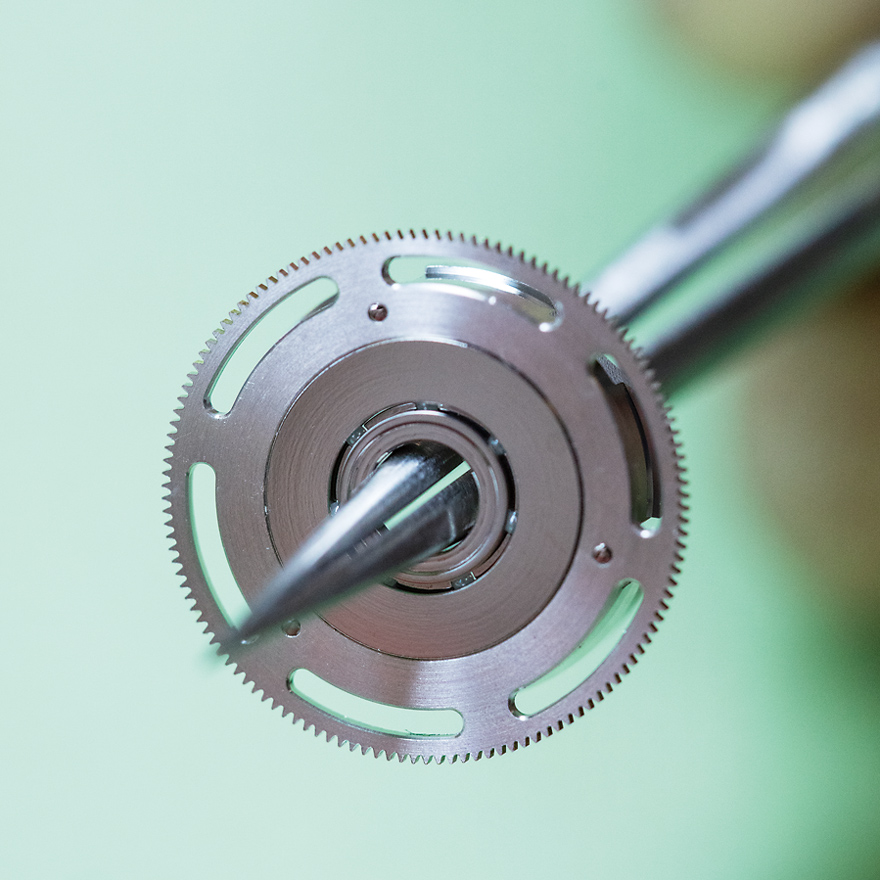
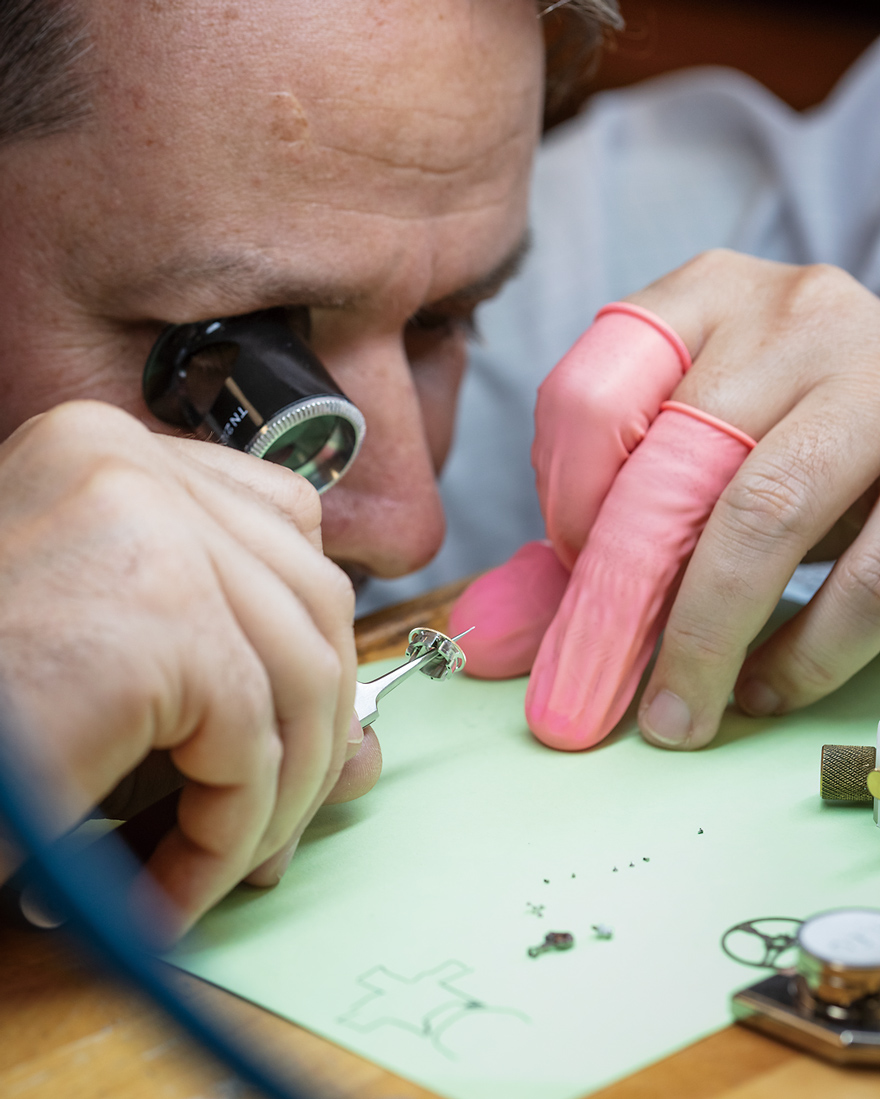
もちろん、ギガ トゥールビヨンを生み出せた背景には、ウォッチランドの進化がある。R&D部門のパトリック・ペレは「チタン製のキャリッジを使えるのは、加工する設備が整ったため」と明言する。もっとも手作業による仕上げ直しも難しいため、片重りを出さないためには、そもそもの加工精度を上げる必要がある。切削上がりの状態でのテンワの加工精度は±10ミクロン以内というから、かなり精密だ。
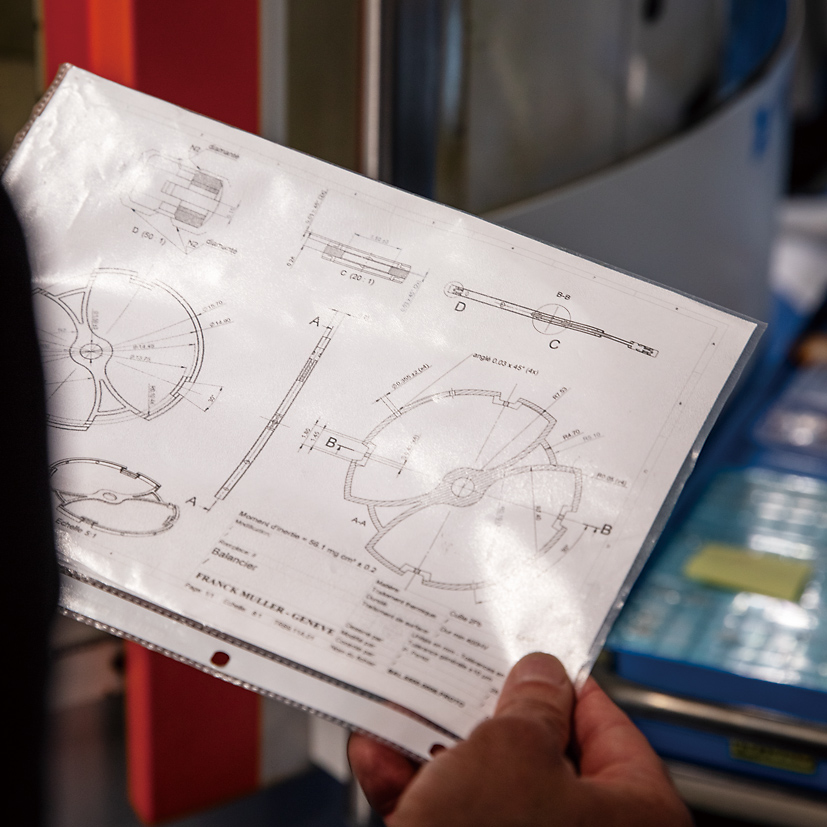
加えてコンプリケーション部門では、フライングトゥールビヨンを支えるセラミックス製のベアリングもチェックしている。同社は2001年のフライングTからボールベアリングを用いてきたが、近年はセラミックスに置き換え、格納するハウジングの精度を高めることでトゥールビヨンの精度をさらに向上させたのである。
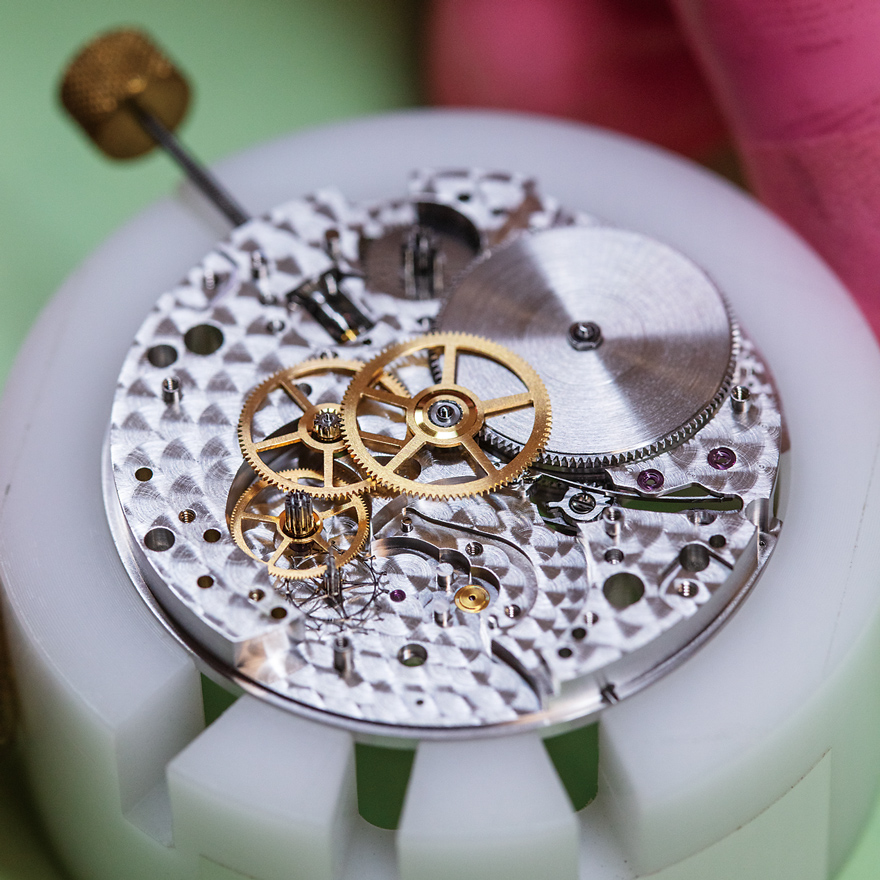
自社製のFM1700系も、やはりトゥールビヨン工房内で組み立てられている。トゥールビヨンに比べて簡単そうに見えるが「傷が付かないようにするのは難しい」とのこと(デスト)。シャトンへの石留めや、緩急針の組み立て(!)、その研磨も時計師が行うというのだから、普通の時計師に委ねられないのは当然だろう。では、仮に傷が付いたらどうするのか?
「組み立て工房の下のフロアにある装飾部門で、再仕上げがすぐにできますよ」(デスト)
ウォッチランドの名の下に高度な融合を果たし、ノウハウを蓄積するフランク ミュラー。どの部門も面白いが、さらに興味を引いたのはカーボンケースの切削と文字盤の保管庫だ。
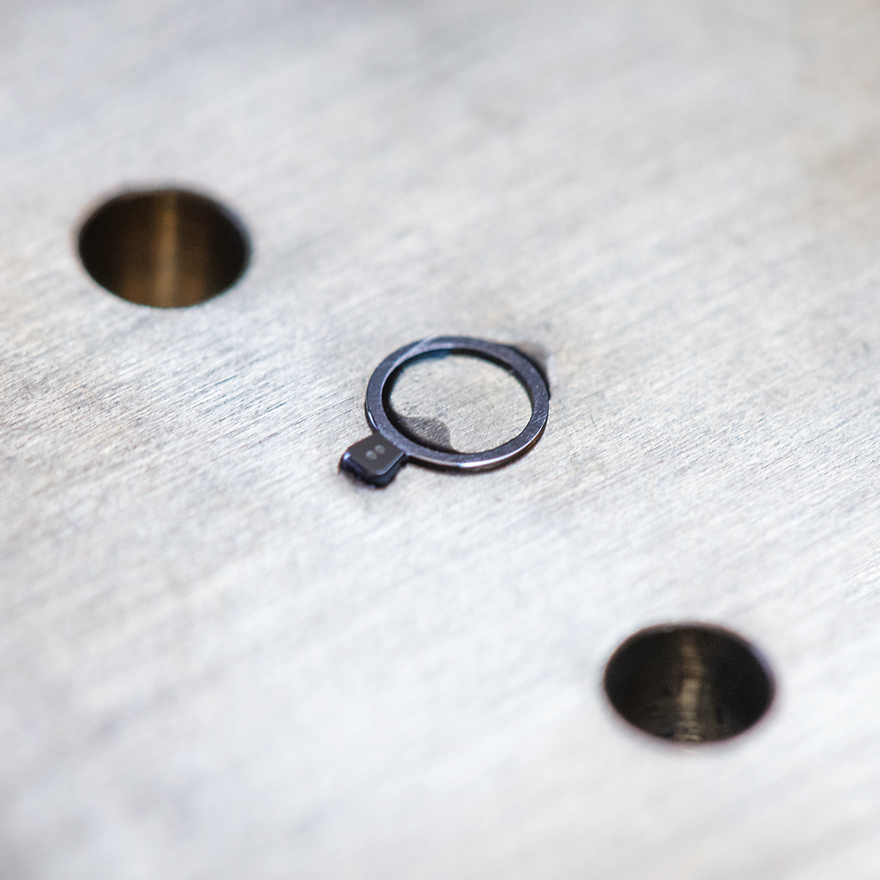
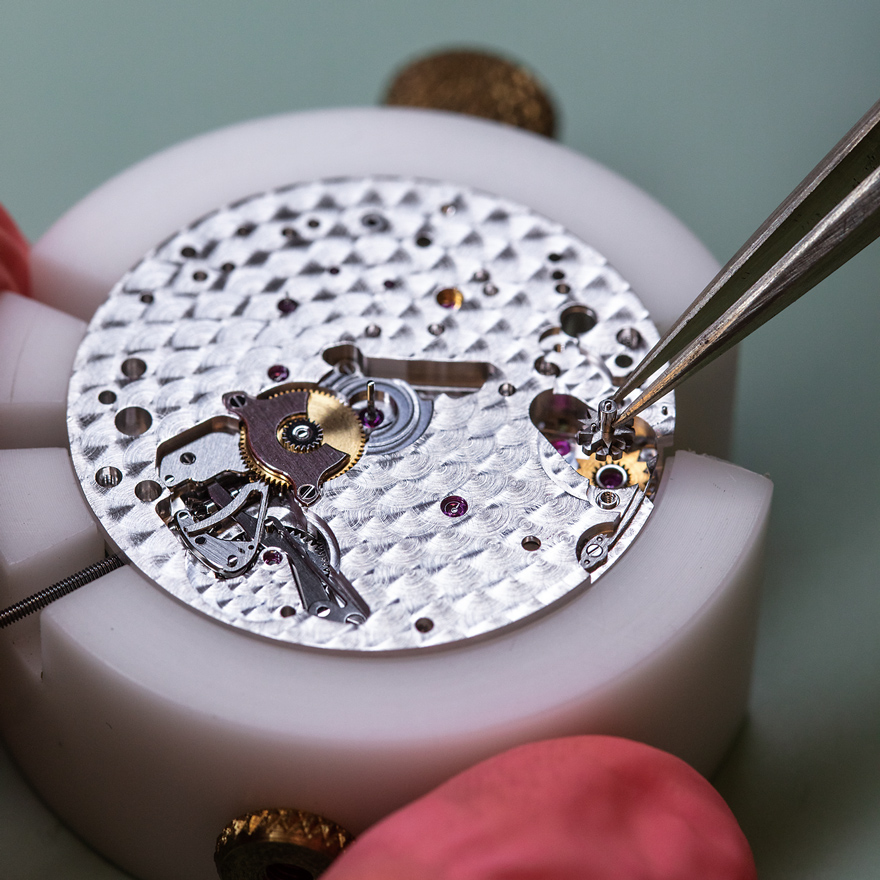
現在、フランク ミュラーのケースは、大部分がグループ会社のジュテック社で製造されている。しかし、プロトタイプや少量生産モデルのケースはウォッチランド内で行われている。その新しい試みが、なんとカーボンケースだ。
長年在籍する熟練工と、新しいフライス盤や旋盤のおかげで、ウォッチランドは部品の加工精度を大きく高めてきた。例えば、地板の加工精度は±2ミクロン(!)以内、研削で仕上げる天真の精度も同様というから、ウォッチランドは、今やスイスでも最も優れた時計工房と言える。とりわけ「切削する際の音や振動で機械を微調整する」というノウハウを併せ持つマニュファクチュールは、筆者の知る限り、ほかにはまずない。
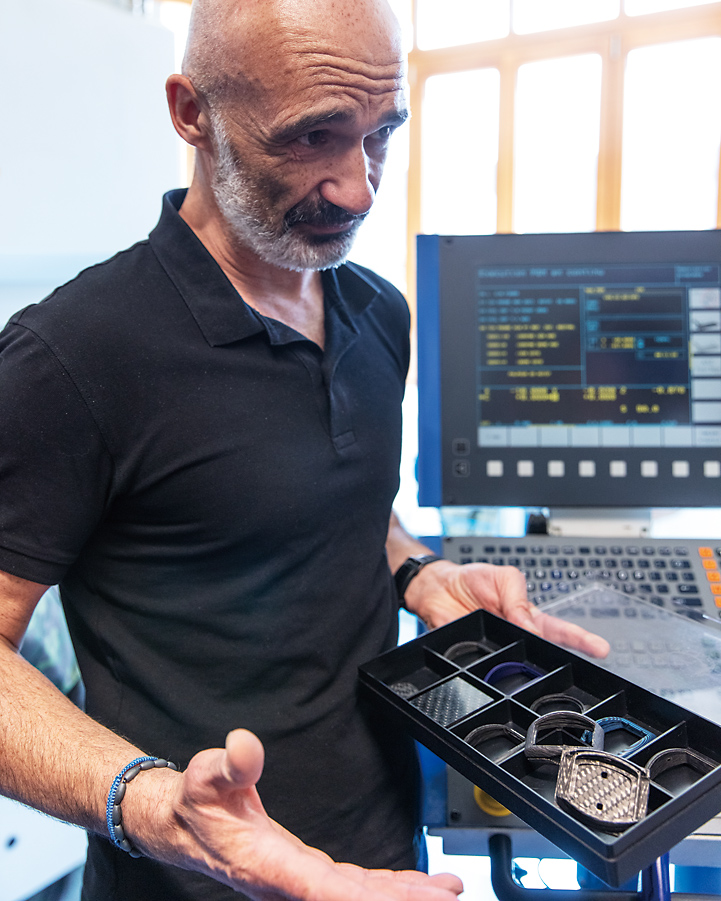
そんなウォッチランドが取り組んだのが、カーボンというウォッチランドにとっての新素材だった。炭素と樹脂で構成されるカーボンは正直、仕上げも素材も玉石混淆である。樹脂を増やせば加工しやすくなるが、耐久性は下がる。逆に炭素繊維を増やすと、硬くなるが加工は難しくなる。また、繊維が飛び出すという問題もつきまとう。
ケース作りにプライドがあるフランク ミュラーは密なカーボンを選び、2年かけて切削の手法をマスターした。担当者は語る。「カーボンは加工時のストレスがかかりやすい素材だ。そのため、繊維を出さない加工が重要になるのです。必要なのは経験だね」。繊維を出さない切削とは初耳だが、そのためにツールや潤滑油を変えたとのこと。「ひとつ切削するのに約2時間半、1日4個から5個しか製造できない」というから、かなりの手間だ。最新の機械に依存するのではなく、必ず職人技が伴っているのが、ウォッチランドらしいポイントだ。
もうひとつの見るべきポイントが、文字盤の保管庫である。ウォッチランドの中枢であるシャトーは、もともとはフランク ミュラーの工房であった。現在はオフィスとして活用されているが、例外として、シャトーに付随する半地下の部屋は、文字盤の保管庫として使われている。
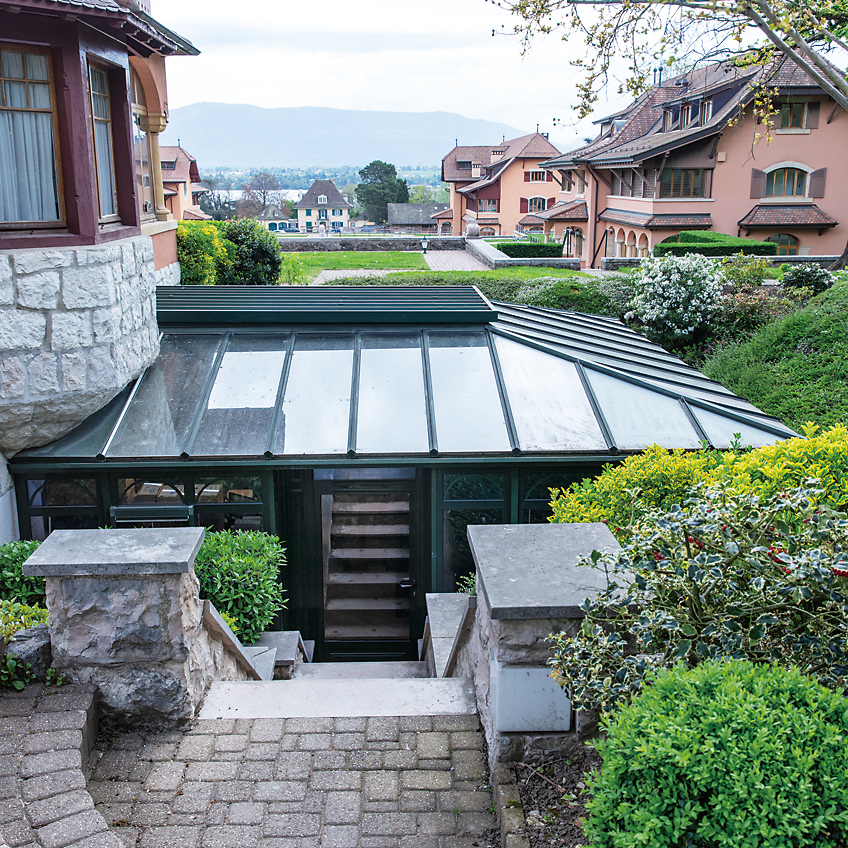
ここに保管されるのは、1992年から製造された約7000種類、合計約100万枚もの文字盤である。つまり、フランク ミュラーの腕時計を彩ってきた文字盤が一通りそろっているのだ。この部門を管理しているのが、アンナ・サリスである。彼女はフランク・ミュラーとヴァルタン・シルマケスが雇った初の社員であり、今なお、生産や納品管理に携わっている。「私がフランク ミュラー初の社員よ」と彼女は笑うが、従業員が長く勤めるフランク ミュラーにあっても、初の社員までもが在籍しているとは意外だった。
彼女に頼むとさまざまな文字盤が出てきた。現行モデルはもちろん、日本限定版や、往年のクロノグラフといった文字盤も在庫されている。しかも彼女は、どこに何があるのかを覚えているのだ。普通はリストを作って厳密に管理するが、人に委ねているのはいかにもフランク ミュラーではないか。
ジュテック社
理想のケースを形作る金型の精度
フランク ミュラーが成功を収めた最大の理由は、間違いなくフランク・ミュラーという時計師の存在にある。しかし、優れたケースがなければ、今ほどの成功は得られなかったのではないか。フランク ミュラーの造形を支えてきたのは、ラ・ショー・ド・フォンにあるケースメーカーのジュテック社だ。同社の強みは、切削ではなく鍛造でケースを作ること。立体的な造形には向かないとされる手法を同社は磨き上げ、今やフランク ミュラーには欠かせない存在となったのである。
フランク ミュラーは、ほとんどすべてのモデルに冷間鍛造(=プレス)で仕上げたケースを使っている。切削が当たり前になった今では極めて珍しいスタンスだ。もっとも、フランク ミュラーの共同創業者であるヴァルタン・シルマケスが、かつて鍛造でケースを作る第一人者だったことを考えれば、このスタンスは当然だろう。鍛造では絶対に不可能とされた、トノウ カーベックスケースを実現したシルマケスは、スイスの時計業界がほとんど諦めてしまった鍛造に、今なお可能性を見いだしているわけだ。
フランク ミュラーのケースの大半を製造するのが、ラ・ショー・ド・フォンに位置するケースメーカーのジュテック社である。創業は1971年。フランク ミュラーの創業間もない頃から鍛造でケースを製造していたが、2007年にフランク ミュラーに買収された。当時、フランク ミュラーには2社がケースを納入していたが、同じ鍛造によるケースでも、ケースに鬆(す)の入りにくいジュテック社が選ばれたのである。
同社製造部長のナワリ・ネジブは、鍛造のメリットをこう語る。「NC切削でケースを作ると時間がかかってしまうのです。対して鍛造は時間を短縮できるし、ケースも丈夫になり、面がきれいになりますね。その半面、製造工程の管理は難しくなります」。今のジュテック社の実力を示すのが、風防を固定する段差だ。普通は切削だが、ジュテック社は鍛造のみで階段状の凹みを作っている。これができるのはスイスでもジェテック社だけ、とネジブが豪語するのは当然だろう。
ジュテック社では最初に、ステンレススティールの場合は54トンでケースの原型を抜き、続いて22トンの圧力をかけてケースの原型を成型していく。2.5mmから15mmの厚さの板をプレスで抜けるのは、スイスでもジュテック社のみというからそのノウハウは類を見ない。その後、いったん120トンでケースの大まかな形を作り、10トンまで圧力を下げ、再び20トンに上げ、最終的には50トンの圧力でケースに仕上げていく。ひとつのケースを作るのに必要な工程数はおよそ30から40、仕上がりには約4週間かかるというから、切削よりも時間がかかっている。
もちろん、これらのプロセスには、熱処理の工程も含まれる。ステンレススティールの場合は1080℃で25分、温度を下げてトータル40分、ゴールドでは700℃で30分といった具合だ。これを3名のプレス職人、そして機械を調整する2名のみで回しているというから驚かされる。
面白いのは、極力切削のプロセスを省こうとしている点だ。そのため、ジュテック社の工房では、ケースを0.1mm薄くするためだけに、プレスをかける場合があるという。現在は、ケース内側の段差も、プレスで付けようと試みているというから、今の時計業界では類を見ない。ちなみに、グランド カーベックスケースは、ケースの一部に切削を加えているが、それ以外のモデルは、基本的に外側を切削しない。鍛造だけで面と精度を出せるのは、よほど自信があるからだろう。事実、ゴールドケースの不良品率はゼロ、ステンレススティールケースでも500個に数個程度しかないという。
もっとも、これだけ技術があると、ウォッチランドからの要求はさらに厳しくなる。それが、グランド カーベックスのチタンケースだ。筆者はチタンケースだけは切削だと思っていたが、実は鍛造で仕上げたものである。「ジュテックではチタンも鍛造で仕上げています。最初の段階でかけるプレスは60トン、熱処理の時間は10分ですね」(ネジブ)。しかし、チタンケースを鍛造で仕上げるのは理論上極めて難しい。スイスのメーカーで鍛造を使っている会社は、おそらくほかにはないはずだ。
「確かにチタンは金型にくっつくため、加工は難しいのです。ですから、特別な油を使い、温度を上げて叩くようにしています」。チタンケースさえ鍛造で成型できるジュテック社は、今も新たな素材の鍛造を試行錯誤しているという。「ブロンズ素材のケースを鍛造で作れと言われたけれど、さすがにそれは無理だから断りました」(ネジブ)。
加えて、ジュテック社は、3軸プレス機なるものも導入した。これは立体的にプレスを加えるのではなく、3カ所の軸でプレスの圧力を変えられるというものだ。そのため、3つある工程をひとつにまとめられるという。また、複数箇所で圧力をかけられるため、ヴァンガードのような大きなケースにも適応できる。あくまでもプレスの技術を磨き上げるのが、ジュテック社のやり方であるようだ。
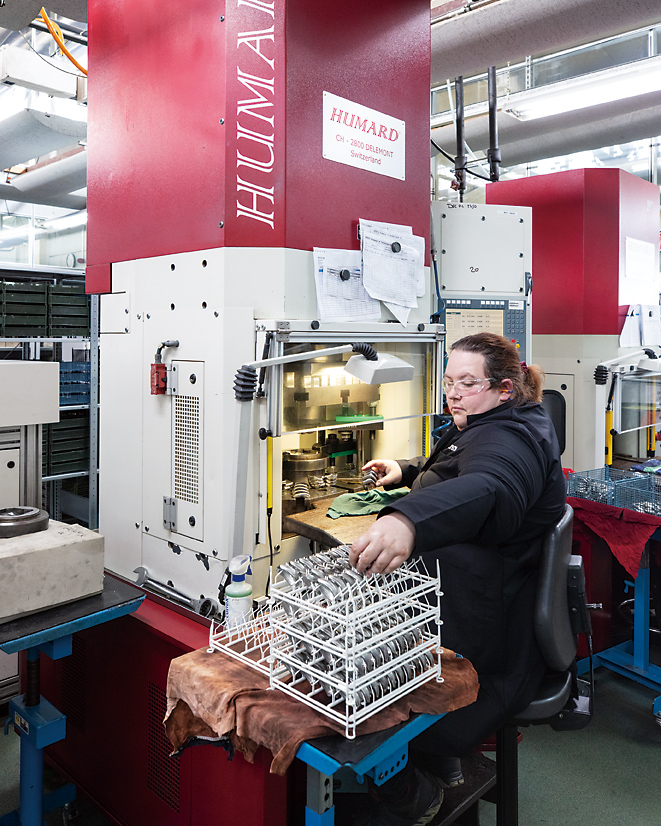
さらに、ジュテック社のユニークなノウハウはプレスに限らない。プレスに必要な金型の製造も、他社とは一線を画している。MIKRONとYASUDAの電気溶解器を使い、銅製の原型を押し当てて金型を作るのは他のメーカーに同じ。しかし、ジュテック社の金型責任者は、スイスでは珍しく35年ものキャリアを持っている。「金型は使うたびにメンテナンスしますが、1000個ケースを抜くとダメになりますね。ちなみに、金型を作る銅の原型は、寸法の公差が100分の1mmから破棄です。金型も最大100分の2mmの公差ですね。一般的な切削より精度は出ていますよ」。
ウォッチランドに劣らず、極めてユニークな工程を誇るジュテック社。ここでも際立つのが、自らの仕事に誇りを持つ、熟練工たちの姿であった。
冷間鍛造+熱処理
ジュテック社では、基本的にケースをほぼ鍛造だけで成型している。スイスでも極めてユニークなケース製法が残った理由は、鍛造で切削以上の精度を出せるためだ。しかも同社は、鍛造の土台となるブランクさえも、自社で製造している。圧力のかけ方、熱処理の温度や時間、そういったすべてのノウハウが、フランク ミュラーにユニークなケースをもたらすこととなった。
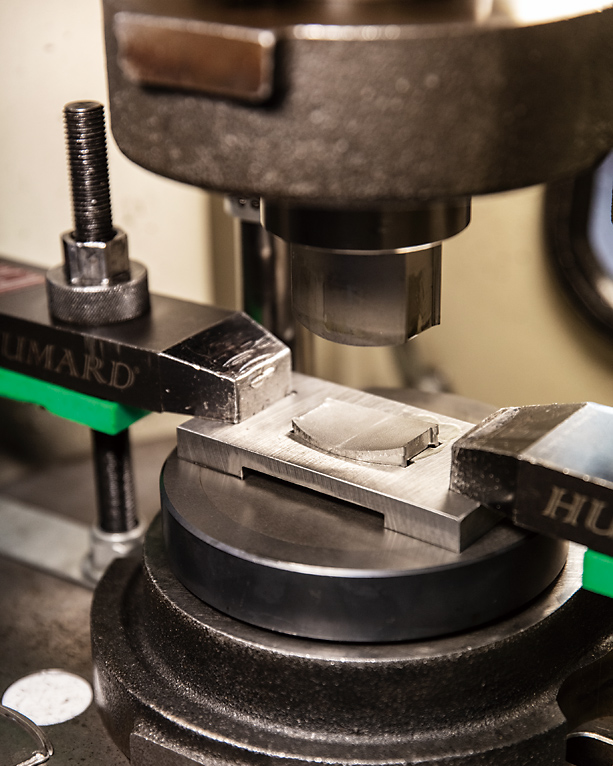
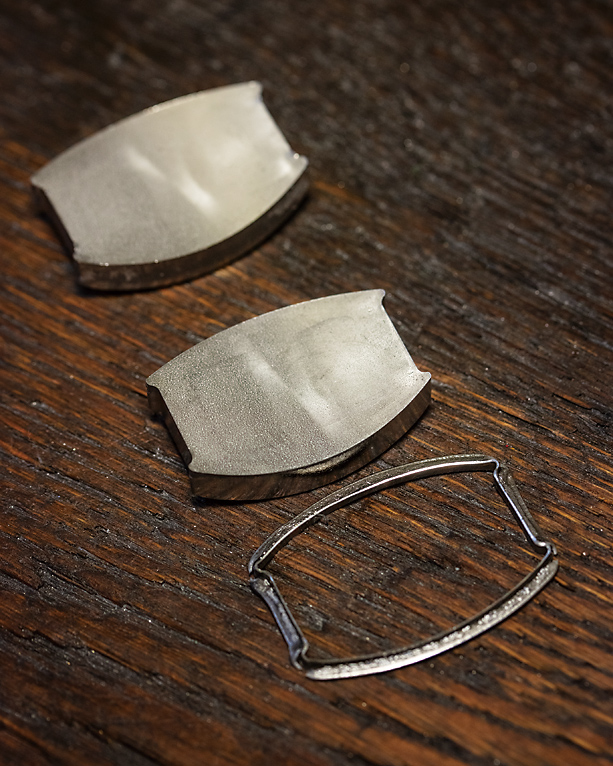
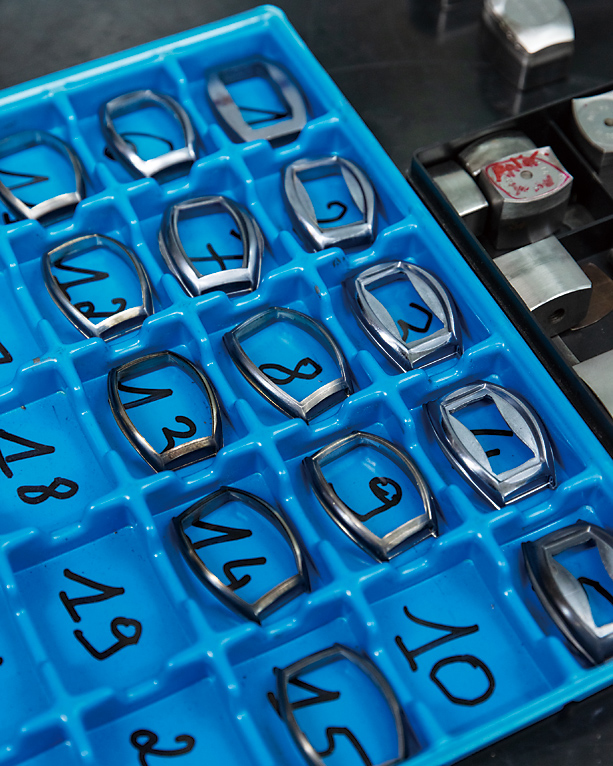
3軸プレス/品質検査/研磨
鍛造の技術を磨きあげてきたジュテック社は、近年、まったく新しいプレス機を導入した。その理由は、大きなケースを鍛造で打ち抜くため。プレスにもかかわらず、ケースの公差が0.03mm以内という驚くべき精度は、鍛造で切削以上の精度を出す、という同社の姿勢がもたらしたものだ。結果として、ジュテック社のケースは、より高い品質を備えるようになった。
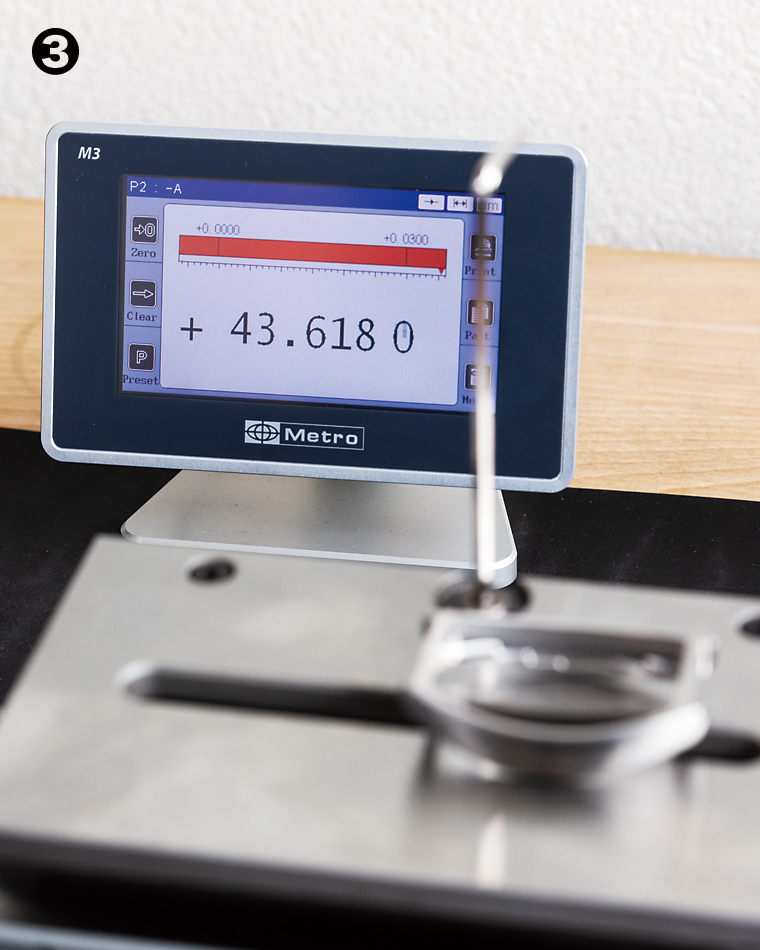
金型
鍛造の鍵となるのが、金型である。スイスの時計業界では見ることの難しくなった金型に対するノウハウが、ジュテック社にはまだ色濃く残されている。1/100mmの精度で製造される金型や、プレスのたびにメンテナンスするという姿勢が、ケースの精密な仕上がりを支えている。しかも同社は、将来のメンテナンスを考えて、過去のモデルの金型も完全にストックしている。
フィル・ダーノルド・リンデール社
フランク ミュラーたらしめる文字盤作りの秘技
創業間もない頃からフランク ミュラーの文字盤を製造してきたのが、フィル・ダーノルド・リンデール社である。高級時計の文字盤を製造してきた同社は、フランク ミュラーの傘下に入って以降、その技術力をもって、フランク ミュラーの文字盤を大きく変えてきた。基本的なプロセスは、多くの文字盤メーカーに変わりない。しかし、随所に見られる違いが、フランク ミュラーの文字盤に唯一無二の個性をもたらすこととなった。
フランク ミュラーのアイコンといえば、大きく湾曲したトノウ カーベックスケースと力強いビザン数字があしらわれた、やはり大きく曲がった文字盤だ。この文字盤を製造するのが、フランク ミュラーの傘下にあるフィル・ダーノルド・リンデール社である。1974年創業の同社は、当初、一部の宝飾ブランドに文字盤を納めていたが、99年にフランク ミュラーの傘下に収まり、現在はフランク ミュラーとバックス & ストラウスの文字盤だけを製造するようになった。従業員数は100名というから、専業の文字盤工場としてはかなりの規模だ。
同社の責任者を務めるのは、アラン・ヴィオネだ。自動車の技師などを務めた彼は、買収したボイヤ家に呼ばれて入社し、機械工としてキャリアを重ね、今や同社の責任者となった。
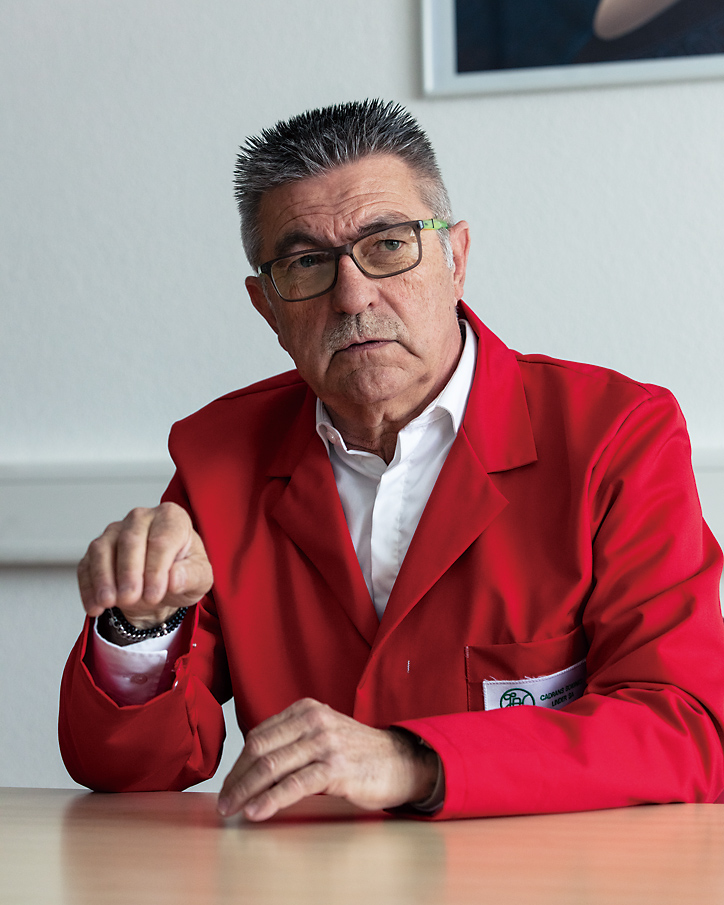
「90年代後半、フランク ミュラーが新規の文字盤メーカーを探していたのです。たまたまボイヤの甥がフランク ミュラーに勤めていた縁で、リンデールが文字盤を作るようになりました」
以来、リンデール社がフランク ミュラー向けに製造した文字盤は少なくとも3万種類。2024年の新製品だけでも、650種類の文字盤を作ったという。そんな同社の強みは、言わずと知れた分厚いエナメル塗装仕上げの文字盤だ。しかし10年前からはPVD仕上げも採用するようになったという。新技術の採用が加速した理由は、技術部門の責任者であるトリスタン・カタンのおかげだ。マイクロテクノロジーと製造プロセスの学位を持つ彼は、地元企業のリンデール社に就職し、その革新を後押ししている。もっとも、同社で見られる職人技と最新技術の融合は、ウォッチランドやジュテック社にまったく同じである。
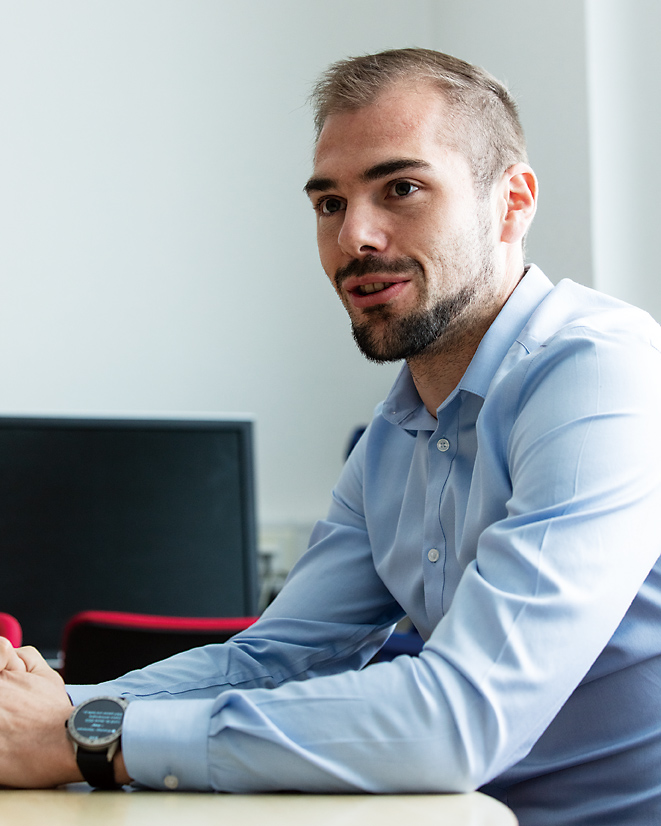
まず驚かされたのが、文字盤にスタンプギヨシェを施すプロセスだ。文字盤にギヨシェ模様の凹凸を付けるために、1950年代の電気式プレス機を使っている。油圧式では細かい模様を付けられないため、グランド カーベックスが採用する文字盤のギヨシェ模様は電気式プレス機でないとくっきりと出ないという。その後、丸いブランクはケースに合うように型で抜かれ、固定用の足が取り付けられる。ここでも使われるのは、50年代の古い機械だ。
足が付けられた文字盤は、次のプロセスで大きく曲げが入れられて、メッキと塗装の工程に回される。フランク ミュラーでは色付けはメッキかPVD、あるいは塗装で行い、その上から保護用のクリアを20〜40ミクロン程度かけるとのこと。省力化のために塗装の工程は一部自動化されているが、140℃まで温度を上げた恒温槽で最低8時間保管し、塗料の溶剤を完全に抜くという入念さだ。担当者は「時間を尊重しないと、良い文字盤は作れない」と語る。
この工房で最もフランク ミュラーらしさを感じさせるのはアプライドのビザン数字を作る工程だろう。なんとすべてのインデックスは足を付けた板ではなく、真鍮のブランクを足ごと(!)切削したものだ。マシニングセンターを使って、インデックスを削り出している。あえて手間のかかるプロセスを選んだ理由は精密に取り付けるため。切削されたインデックスは自動機械か手作業で曲げを付けた後、磨いて鏡面に仕上げていく。10年前はほとんどなかったプロセスだが、立体感を求めるために近年増えているという。
加えてリンデール社では、このアプライドインデックスにも色を乗せるようになった。インデックスにメッキなどをかければいいように思うが、あえて手作業のペイントを選んだのは、よりボリューム感を出すためだ。熟練工でも最低15分はかかるというから、かなりの手間である。
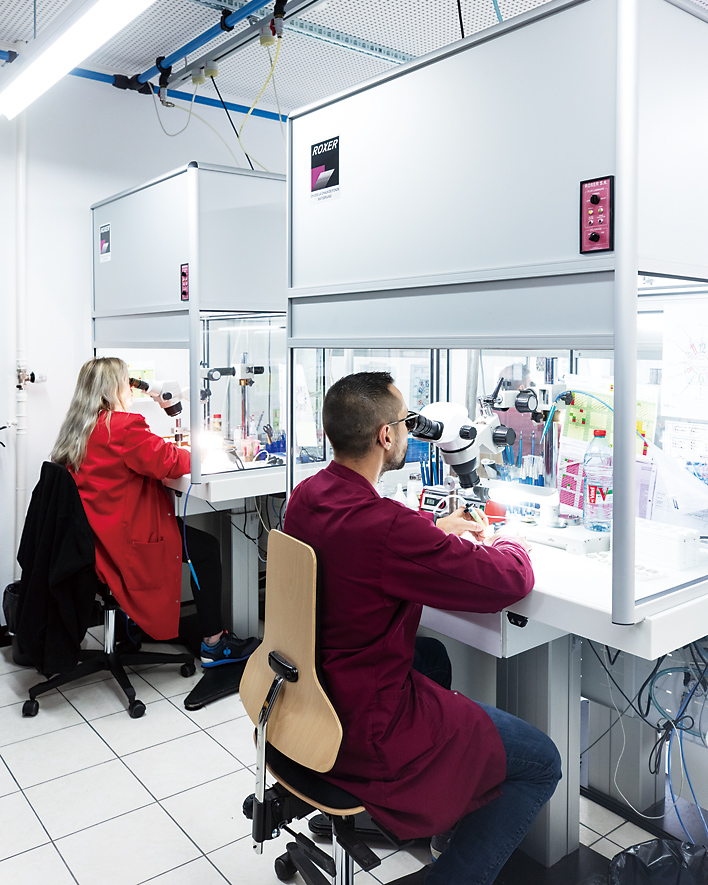
フランク ミュラーの文字盤が独特の光り方をするのは、文字盤の磨きに時間をかけるためだ。例えば、ソレイユ模様を施した文字盤は、曲げの前の段階で、下地が鏡面に整えられる。理由は、模様を付けた後に仕上げを加えるのが難しいため。普通は下地処理の後に磨くことはしないが、あえて下地処理後にアプライドのインデックスを磨き、先の下地をマスキングした後に他のメッキを施すことにより、ツートーンのレリーフダイアルができる。結果、アプライドインデックスと文字盤は見事になじむようになった。
意外だったのは、同社の一角に設けられたPVD処理の工程だ。「普通、PVDを使うと、色はブルーやブラウンが多いのです。でも、ここの文字盤は99%がノワール(黒)」とのこと。ラッカーに技術を持つリンデール社は、よりマットな仕上げを求めて、なんと2014年からPVD処理の文字盤に取り組んできたのだ。まさかフランク ミュラーの一部の黒文字盤が、時計業界でもようやく広まりつつあるPVD仕上げとは誰が想像しただろうか?
熟練工と最新の工作機械が作り出す唯一無二の文字盤。「マスター オブ コンプリケーション」という謳い文句は、実のところ、マスターたちの仕事の集大成なのである。
1. スタンピング
ジュテック社に同じく、リンデール社でもプレス機が活躍していた。上の写真は、文字盤のブランクを打ち抜く電気式プレス機。1950年代のオストワイラー製である。これで丸いブランクを打ち抜くほか、文字盤にパターンを施していく。徐々に力が加わるため、金型への負荷は小さいという。
2. 足付け
プレスで型抜きされた文字盤は、まずケースに合うように外側を6トンのプレスでカットされる。その後、ジグやムーブメントに固定するための足が取り付けられる。大量生産に向けて自動足付け機も導入されたが、今なお少量生産のモデルは、手作業で足が取り付けられる。1950年代に作られたPUETSHIの工具で足をハンダ付けした後、カシメて固定していく。
3. 曲げ付け
足が固定され、穴も開けられた文字盤は、ケースに合うように大きく曲げられる。ジグに文字盤を置き、その上からラバーの薄い板を被せ、約2トンの弱い圧力でゆっくり曲げを入れていく。曲げるためのプレス機は3台あり、文字盤の厚さによって使用する機械を替えているという。
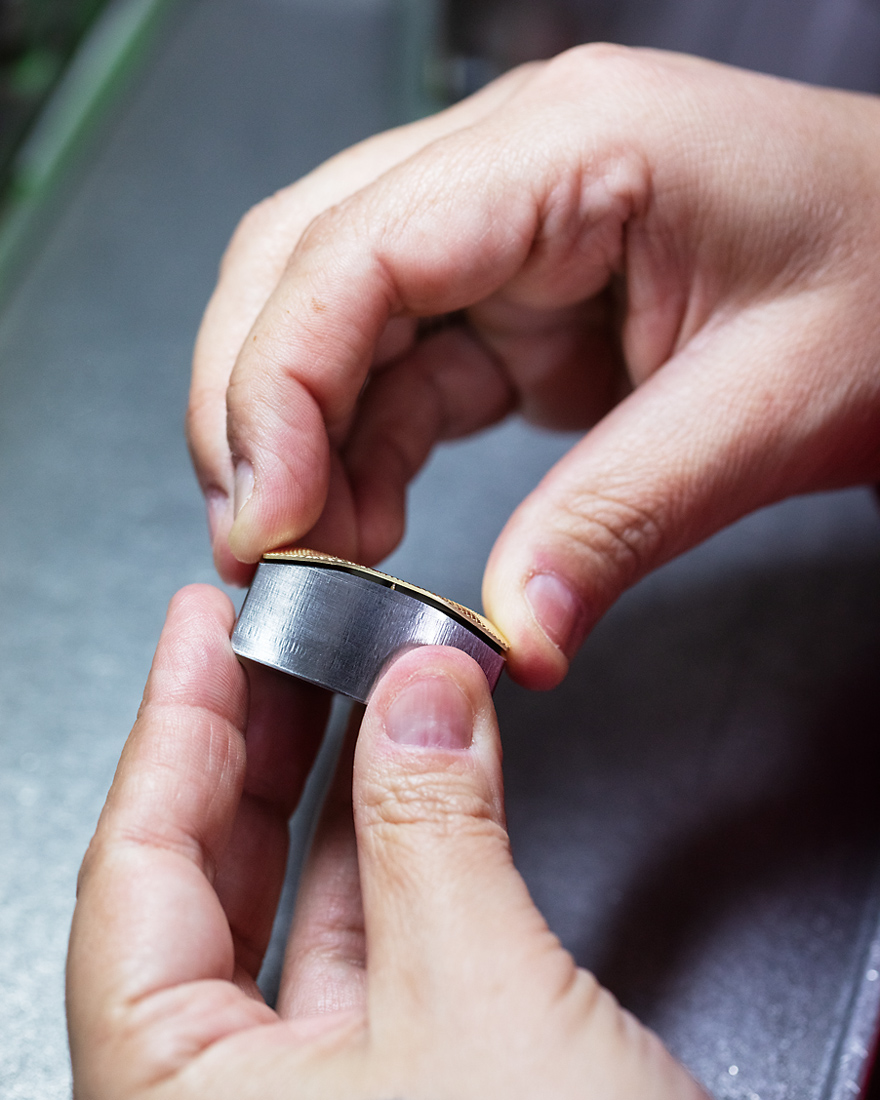
4. メッキ
リンデール社ではメッキも社内で行っている。出せる色は主に金、銀、そしてロジウムとのこと。黒も可能だが、真っ黒にならないうえ、表面に施すラッカーとの相性が悪いという。写真の溶解液に浸ける工程を含めて、1枚の文字盤を完成させるのに、150~200工程が必要になる。しかし半分は破棄され、さらにウォッチランドで2~3割ははねられるため、使える文字盤は2割から3割程度とのこと。
5. 塗装
金、銀、ロジウム以外の色は、基本的に塗装で施される。リンデール社では現在、マシンによる自動塗装と手作業による塗装を併用しているとのこと。塗装を終えた文字盤は、140℃の恒温槽で8時間寝かせて、溶剤を完全に飛ばす。一方、メッキで仕上げられた文字盤には、表面を保護するために20~40ミクロン程度のクリアエナメルが吹かれる。塗料はベルラック製だ。
6. 印字
塗装やメッキが施された文字盤には、印字が転写される。半自動機械も導入されたが、大部分は今なお手作業だ。一般的に、インクの転写は2回。しかし、これも作業者の裁量に任されているという。その後、文字盤に施された印字は、80℃という低い温度で焼き付けられる。普通の印字は約30分、大きなビザン数字は約2~3時間かかるとのこと。担当者曰く「凹凸のある文字盤への印字は非常に難しい」。
7. 植字
近年、フランク ミュラーが好んで採用するアプライドのビザン数字。通常のアプライドインデックスは2本の足を取り付けている。対してリンデール社では、真鍮のブロックを足ごと削り出してインデックスとしている(❷)。あえて難しいプロセスを選んだのは、正確な位置に足を設けるため。インデックスの厚みは0.3mm、足の長さは0.7mmだが、インデックスの大きさにより、足の太さは0.2mmから0.5mmまである。
❶~❹はインデックスの加工と研磨の工程。削り出されたインデックスは糊でディスクに固定され、上からゆっくりバフを当てて鏡面に仕上げられる。糊を剥がし、取り出した後にさらに専用のジグに固定し、メッキ処理を施して完成となる(❸)。作業工程がかなり多いため、歩留まりは非常に悪いと担当者は語る。
❺~❽はインデックスを取り付ける工程。12名の職人が文字盤のふたつの穴にインデックスの足を差し込み、曲がりを調整して文字盤に密着させている(❺)。その後、裏側に飛び出したインデックスの足を削ることで文字盤に固定される(❽)。❼は植字された文字盤の裏側。わずか5分で作業が終わるのは熟練工なればこそ。
8. インデックスペインティング
アプライドのビザン数字インデックスを強調するため、リンデール社では一部モデルのインデックスに色を重ねるようになった。塗料を充填したシリンジをインデックスに当て、色を乗せるのに約15分の時間を要する。
責任者のジェローム・サントスは「色が流れてはいけないし、厚みも出さなければならない。塗料の粘度を出すのは難しい」と語る。色を重ねたら、印字に同じく、80℃の温度を加えて色を定着させていく。上の写真、左のインデックスには縁があるため塗料は流れないが、右のインデックスには縁がないため、表面張力でインデックス上に塗料を留めている。
9. ダイアルスムージング
フランク ミュラーのお家芸とも言えるソレイユ仕上げの文字盤。こういったモデルの場合は、文字盤に加工を施す前に、下地を鏡面に整えている。プレスで模様を付けた後に鏡面仕上げを施すと、模様の凹凸が浅くなってしまうためだ。成型前の平らな文字盤は、上の写真のように回転するジグに固定し、むらなくバフが当たるように磨きを加えていく。地味だが非常に重要な下準備だ。
10. ダイアルポリッシュ
「グランド カーベックス ピアノ」の文字盤を研磨する工程。ジグ(右下)に文字盤を固定し、3回の磨きを加えてエナメル塗装の文字盤を鏡面に仕上げていく。文字盤をフラットにするため、20回も塗り重ねられた塗料を150ミクロンも削るというから、その作業は研磨というよりも研削に近い。
手作業による歪みを嫌って、最後の研磨工程にはRECOMATIC社製の自動機械が用いられている(左上)。これは角度の異なる3枚のディスクに文字盤を当てて磨くもので、リンデール社は10年前に導入。磨き自体は1回2分で終わるが、研磨時の熱でエナメル塗装が溶けないよう、切削のようにたっぷりオイルをかけて磨く(右上)。左下は磨く前の文字盤。エナメル塗装の厚みに注目。
11. PVD
最近、フランク ミュラーで目立つのが、マットなブラック文字盤だ。リンデール社では2014年からPVDの開発に取り組み、現在はブラックの文字盤を製造するようになった。PVDの機械は、オランダ・ハウザー社製のFLEXCOAT HYBRIDである。
担当するミゲル・ダロシャは「この機械では事故的に違う色も出るが、基本的にはブラックしか出せない。そして文字盤に色を定着させるには約8時間かかる」と説明する。「(PVDは)メッキに比べて丈夫で定着率も良いが、機械の調整に30分はかかる」とのこと。また、製造した文字盤の半数は不良品になるという。曰く「半年もすると不良品でゴミ箱がいっぱいになりますね」。
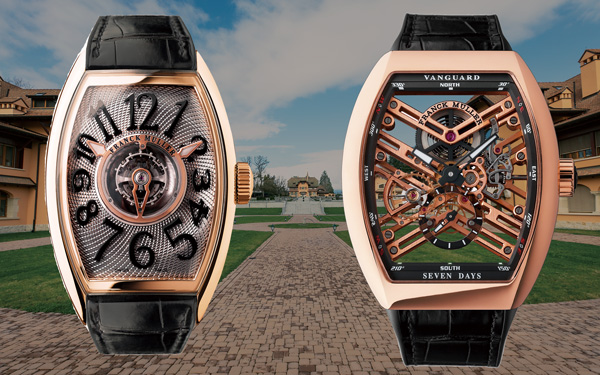
https://www.webchronos.net/features/96949/
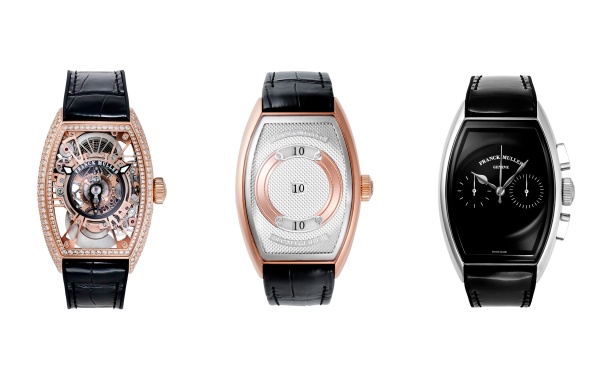
https://www.webchronos.net/features/114033/
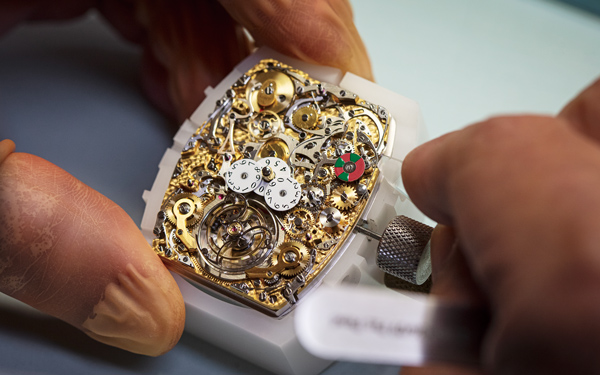
https://www.webchronos.net/features/105502/