F.P.ジュルヌのケースを製造するボワティエ・ジュネーブと文字盤を製造するカドラニエ・ジュネーブは、2022年末、新しい建物に移転した。建物の延べ床面積は2500㎡。1階と2階でケースを、3階と4階で文字盤の製造を行っている。もともと優れた外装を持っていたF.P.ジュルヌの時計だが、移転による拡充でさらにその質を高めるはずだ。
広田雅将(本誌):取材・文 Text by Masayuki Hirota (Chronos-Japan)
Edited by Yukiya Suzuki (Chronos-Japan)
[クロノス日本版 2023年5月号掲載記事]
製法の一新がもたらした、今までにないカタチとクォリティ
2005年に文字盤メーカーを買収したF.P.ジュルヌは、続いてケースメーカーのエリノーを傘下に収めた。11年、F.P.ジュルヌは設備ごと同社をジュネーブに移転させ、社名をボワティエ・ジュネーブに改めた。10年前との違いはその製法だ。移転当初は貴金属の素材を鍛造してケースに仕上げていたが、現在は切削が主流となった。ケースの作り方が一新された理由は、もちろん質である。
鍛造されたブランクを切削し、ケースに仕上げるのはスイスの高級メーカーに同じ。しかし、年産1000本以内という生産本数を反映して、それぞれの作業が入念なのだ。
1階で目を引いたのが、バリ取りの工程である。まずは砂やコランダムなどで下地を均し、続いてガラスを吹き付けて、下地を整えていく。別の部署ではクロノメーター・ブルーに使われるタンタル製のベゼルが下処理を施されていた。職人たちが数種類の砥石を使い、入念にケースの面を均している。ちなみに粘りのあるタンタル素材を磨くと、作業ごとにツールを研ぎ直す必要がある。しかし、17年以降は機械化が進み、手間は減ったとのこと。
機能部品に同じく、ケース製造でもファナックやウィルミンのマシニングセンターが多用されていた。ゆっくりした速度で切削するのも、レニショーの計測ユニットで厳密に採寸するのも同じ。ただし、加工にはかなり時間がかかるとのこと。「トゥールビヨン・スヴラン」のケースを仕上げるには、7〜8時間、セッティングには1時間を要するというから、まったく量産向きではない。
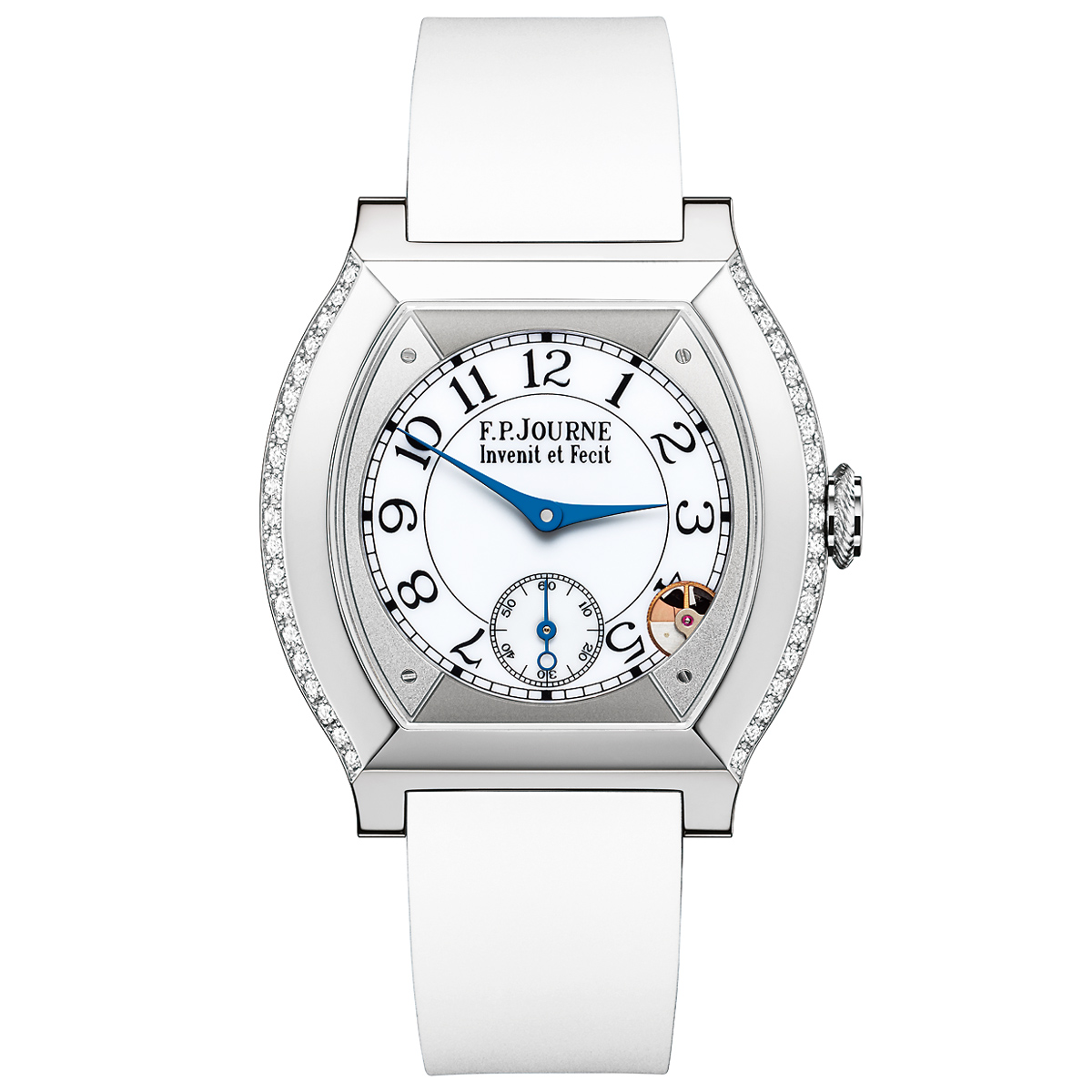
チタン製のケースに38個のダイヤモンドを埋め込んだモデル。自社開発のメカクォーツムーブメントは、電池寿命を延ばすため、約30分静止するとスタンバイモードに入る。自社製の文字盤は夜光塗料を裏打ちしたサファイアクリスタル製だ。メカクォーツ(Cal.1210)。18石。Tiケース(縦40×横35mm、厚さ7.35mm)。3気圧防水。281万6000円(税込み)。
しかし、この手間を惜しまないことで、仕上げは明らかに良くなるという。「最上のツールを使い、設計に忠実に加工することが重要」と担当者が語る通り、ケースの高い加工精度は、F.P.ジュルヌの時計を、好事家向けの上質な時計から、独創的なラグジュアリーウォッチへと変容させたのである。
ケース作りに使われるツールは、ゴム、紙、スポンジなどさまざまだ。もっとも、下準備や仕上げに限らず、どういったツールや新技術を採用するかは現場に委ねられており、十分なテストを経て採用される、とのこと。
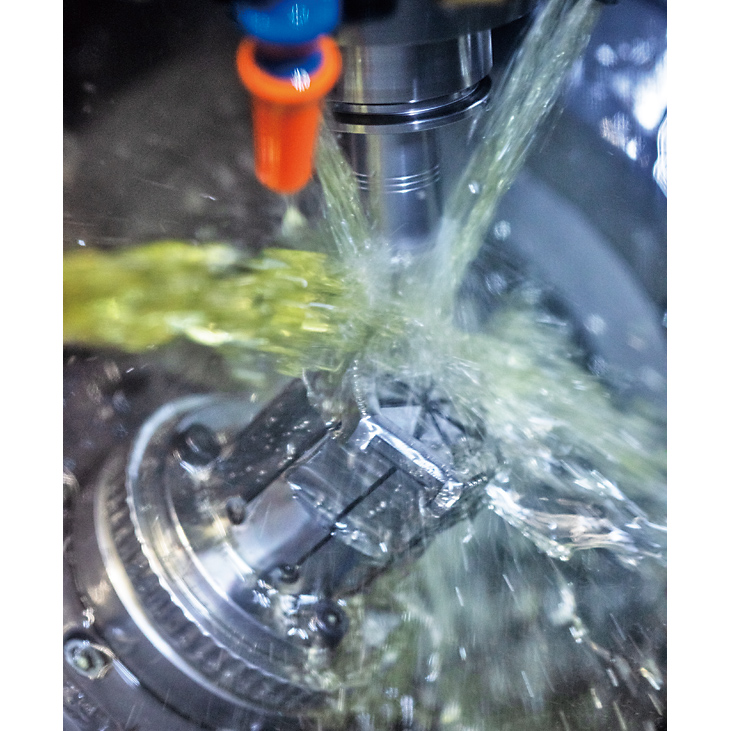
こういう試みで成功を収めたのが、2012年に導入されたレーザーだ。例えばチタン製のベゼルは、2.5mmの深さまで彫れるレーザーマシンを使い、1時間半をかけて刻印を施していく。加えて近年は、そこにリキッドセラミックを充填するようになった。製法はかなり凝っている。
レーザーで彫刻した部品をサンドブラストで荒らした後、リキッドセラミックを充填し、加熱・加圧で気泡を取り、液体に浸けて1時間加熱する。その後、表面を切削すると、セラミックが充填されたチタン製ベゼルが完成する。驚くほどの手間だが、だからこそ天才ジュルヌのアイデアはカタチになるわけだ。
切削と下処理が終わると、最終研磨の工程である。取材時には、タンタルケースが最終工程にあった。もっともゴールドやプラチナとは異なり、下処理でほぼ完全に磨いてしまうとのこと。回転するバフにケースを当てるのは他社に同じだが、ゴールドは1600回転、プラチナは1800回転、タンタルは2400回転と、バフの速度を変えている。また、タンタルではわずかに圧力を加えるのがコツとのこと。
研磨の担当者は「ケースに使われる金属と切削の精度が良くなった結果、以前に比べて最終仕上げの質も改善された」と語る。もっとも、そこで終わらないのが今のF.P.ジュルヌだ。「質は全体的に上がった。しかし、より高めるための改善プロセスを検討中」と言う。質のために製法を一新しただけでなく、さらなる改善を続ける。これが今のF.P.ジュルヌ、なのだ。
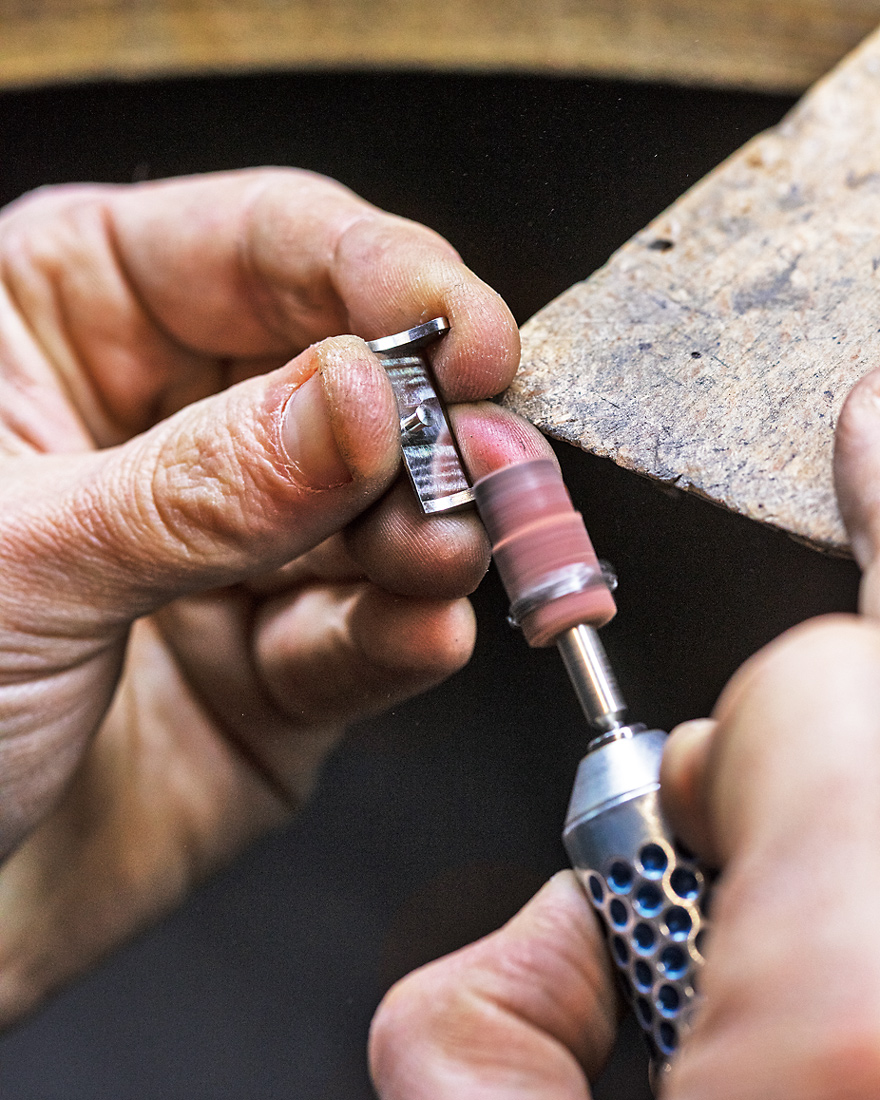
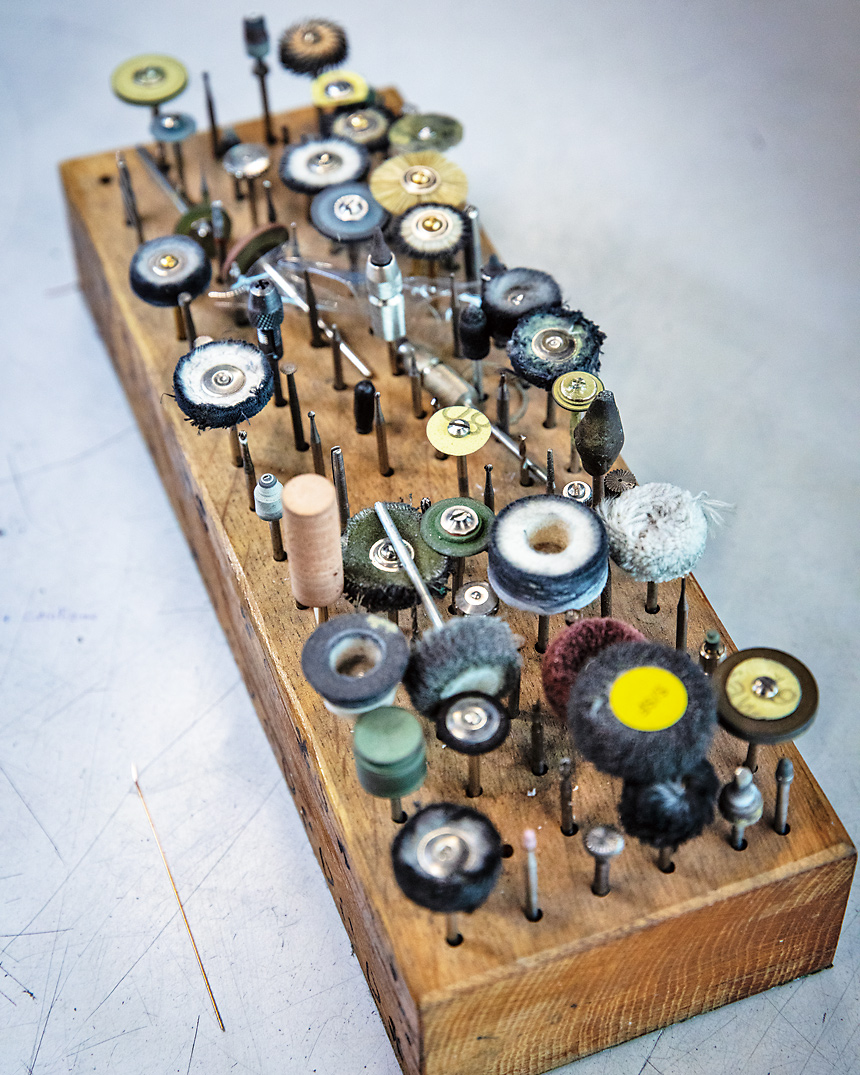
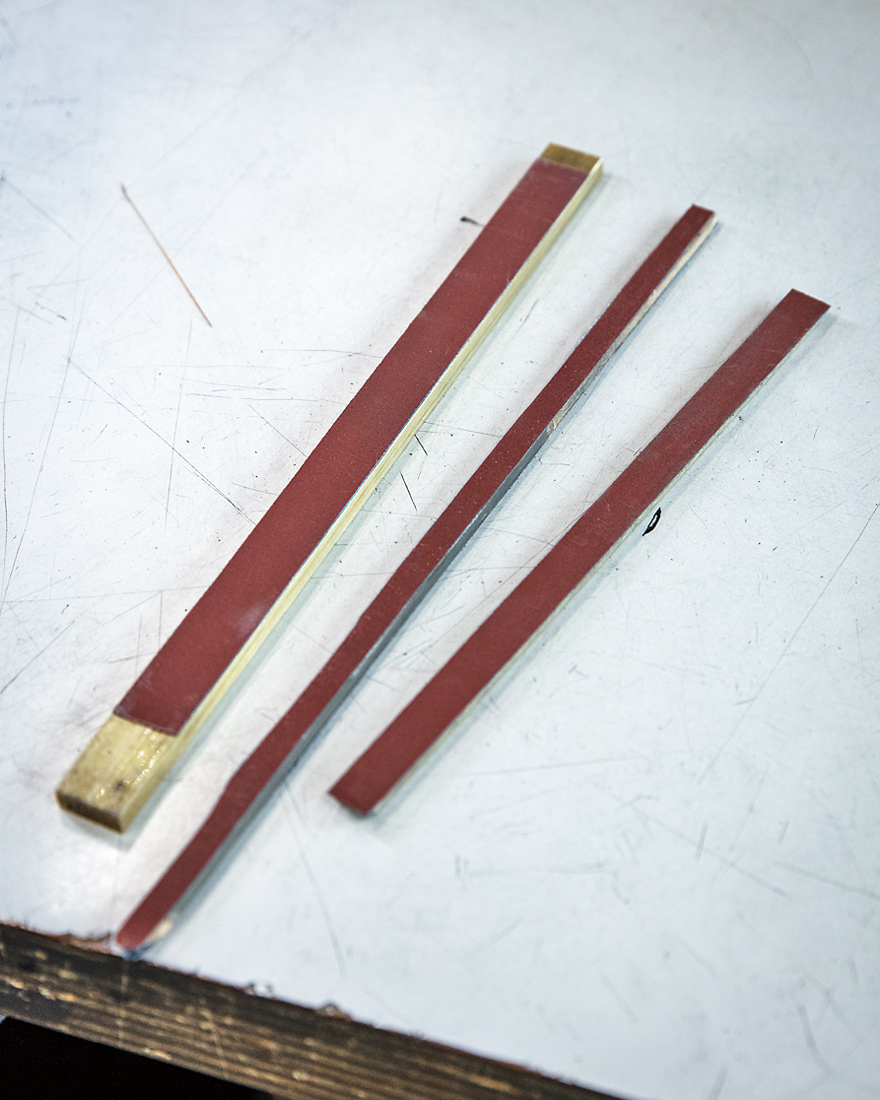
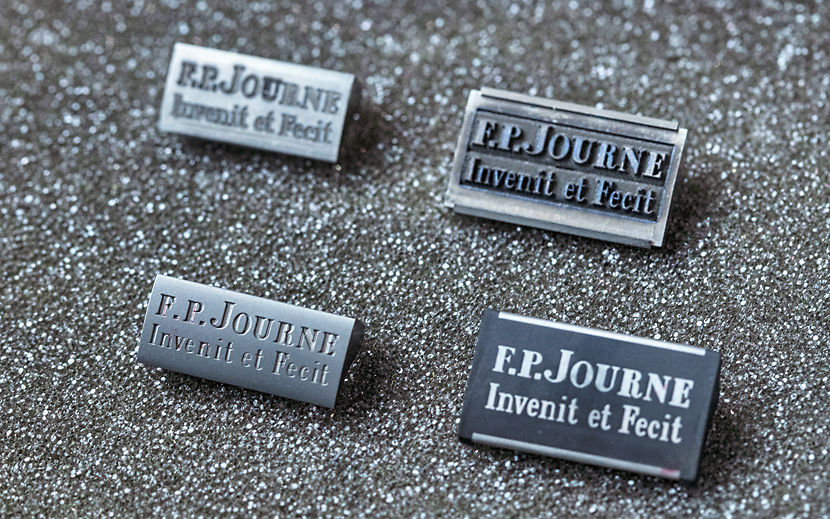
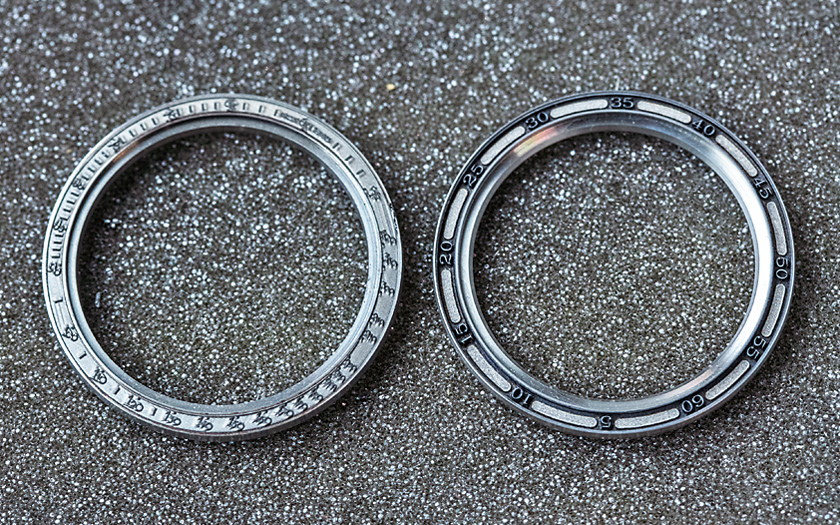
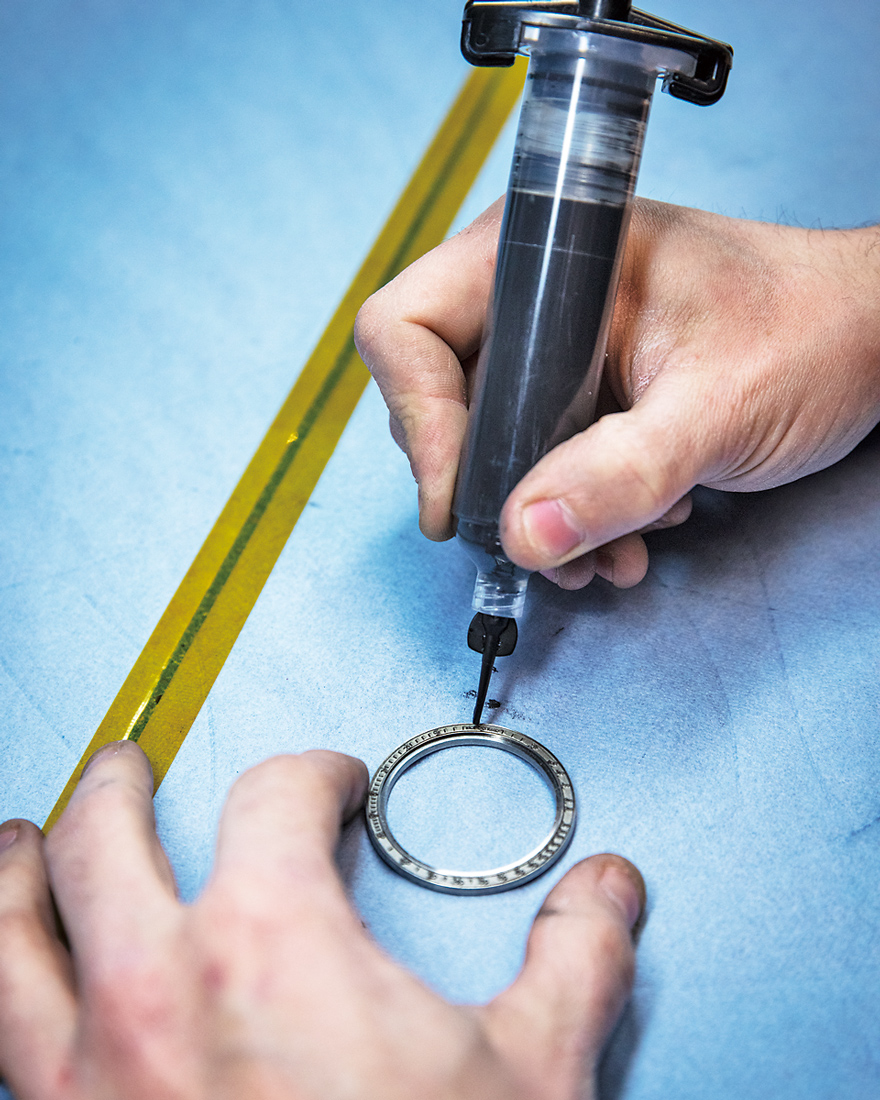
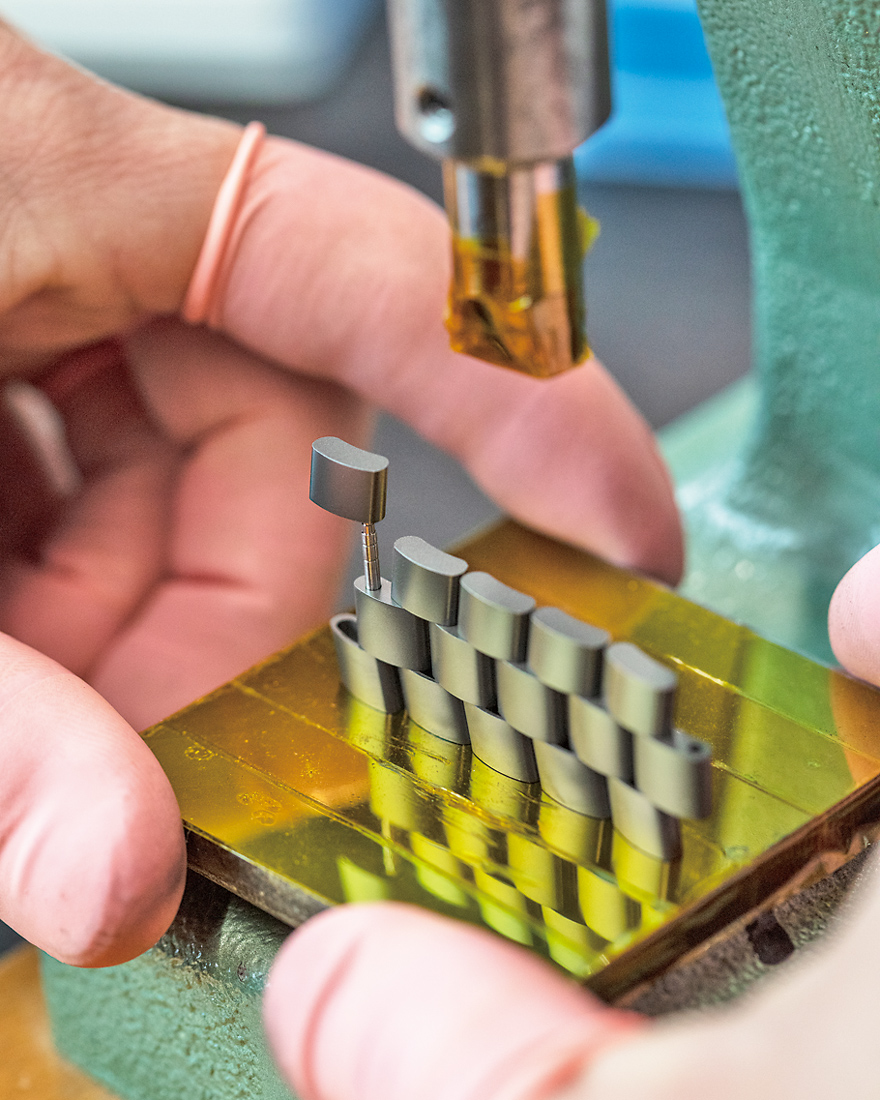
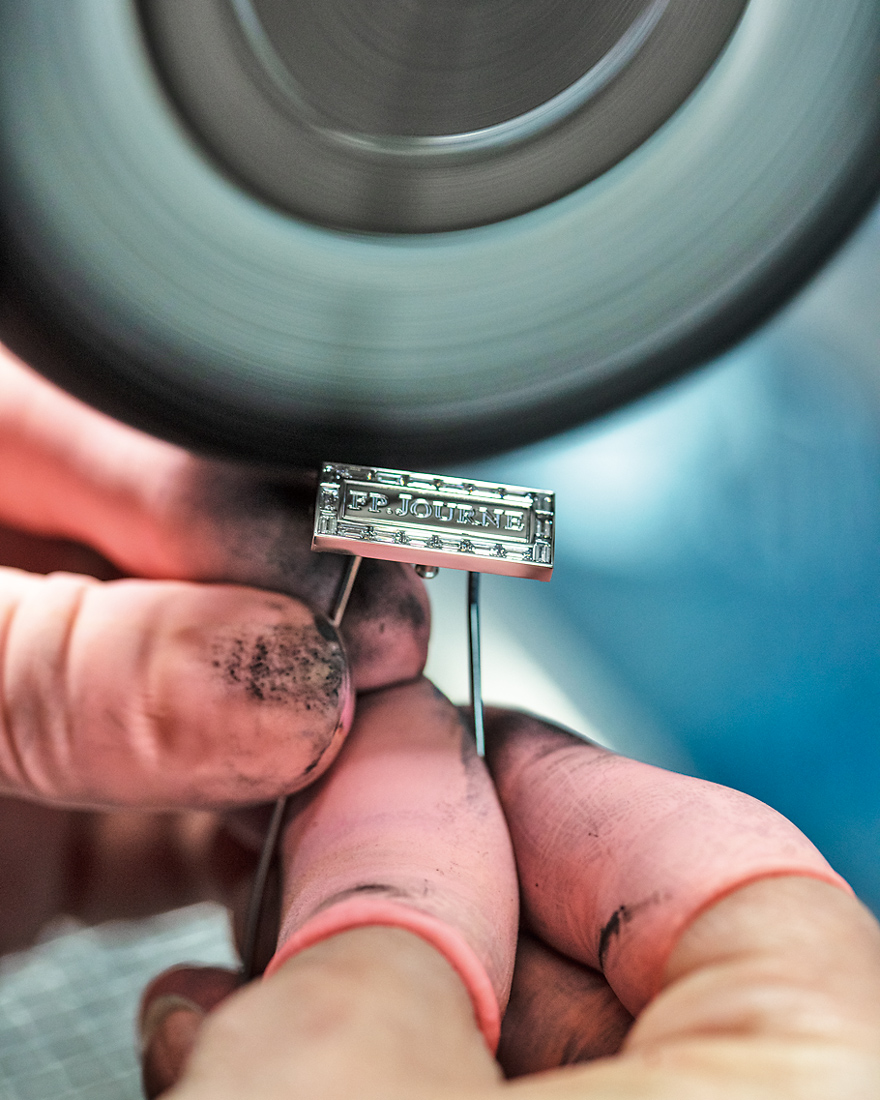
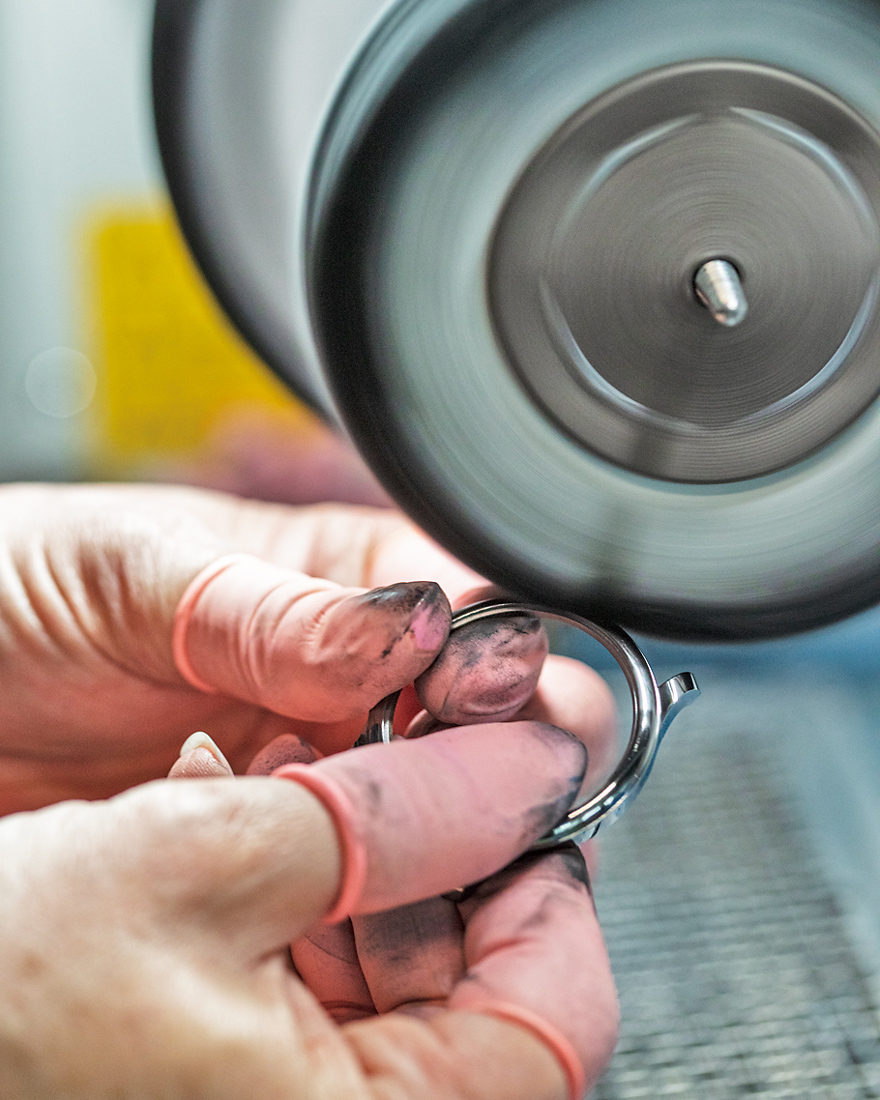
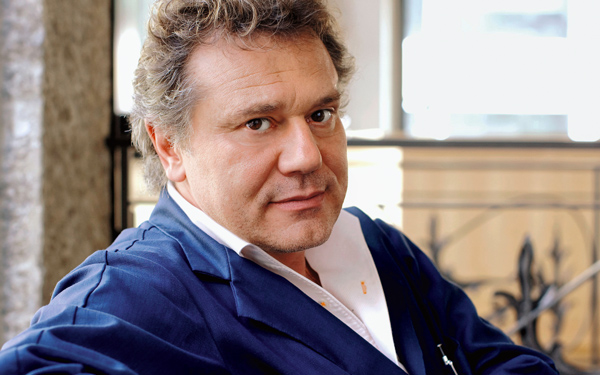
https://www.webchronos.net/features/91928/
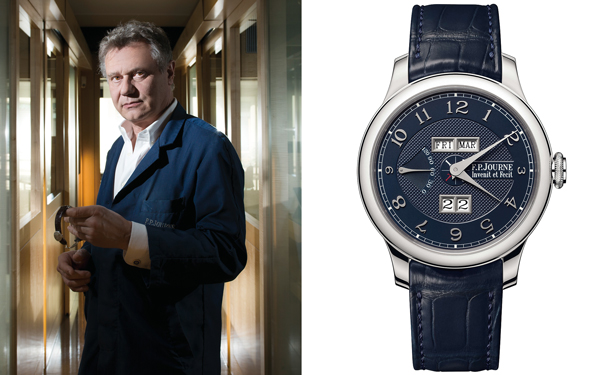
https://www.webchronos.net/features/76482/
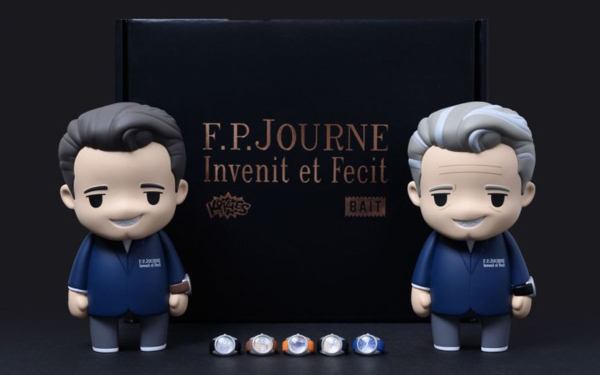
https://www.webchronos.net/features/89473/