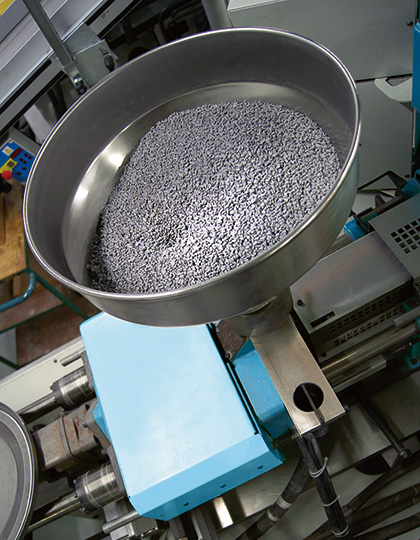
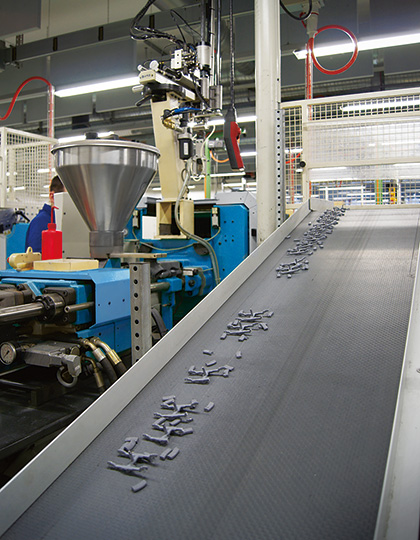
セラミックウォッチ開発の先駆けとして、最前線を疾走してきたラドー。だが、2000年代に入って以降、ラドーが掲げる〝傷付かず、いつまでも美しい時計〟の素材として最適なハイテクセラミックスは、その素材特性が高く評価され、他の時計メーカーでも次々と採用されるようになった。
だが、25年以上も一途にハイテクセラミックスの開発に注力してきたラドーの持つノウハウに、一朝一夕に追い付き、追い越すことはほとんど不可能である。その証しこそが、先述したラドーのマイルストーンモデルのひとつひとつである。では一体、ラドーのハイテクセラミックスは他社と比べて何が違い、何が特別なのか? この点をさらに掘り下げてみたい。
まず、注目すべきは、2012年発表の「ハイパークローム」だ。このモデルは、ハイテクセラミックスを用いたモノブロック構造が最大の特徴である。すなわち、ほとんど射出成型のみで複雑なケース形状をひとつのブロックとして成型することができるのだ。この製法の何が凄いのか?
現在、時計のセラミックケースの製法には大きくふたつの手法がある。ひとつが、ハイテクセラミックスの原料である酸化ジルコニウムをプラスティック(バインダーという)と混ぜ、高温でペースト状の液体にしたものをケースやベゼル、ブレスレットのコマなどの「型」に射出し、1000バールの圧力をかけて成型。その後、圧力と温度を下げて個体化したそれぞれのパーツの原形(モールド)を取り出し、これを1450℃で焼結して完成させる手法。これはラドーやシャネルが採用する量産に適した製法である。もうひとつは、ハイテクセラミックスの塊(ブランク)をCNCマシンによって切削し、ケースを削り出す手法。これはただでさえ硬いセラミックスをかなりの量切削しなければならないため、時間とコストがかかる。ゆえに、100万円以上の高額な高級時計で主に用いられる。
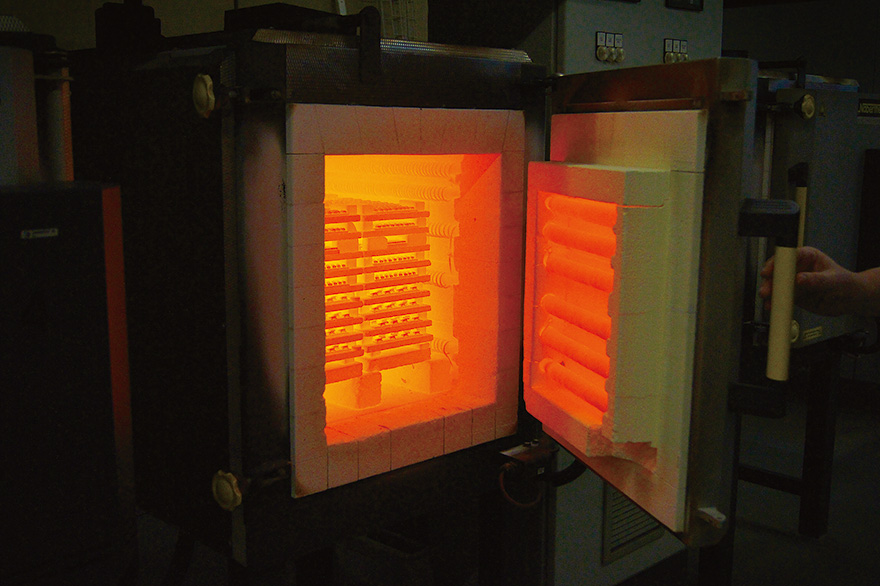