シリコン・モデルノロジー
生産と信頼性をめぐる最新知見
タイプ20の第6世代機にあたる「タイプXXII」は、7万2000振動/時という超高振動によって、圧倒的な高精度を実現した。
それを支えたのが、効率に優れるシリコン脱進機である。
いかにしてシリコンは実用化され、量産化の道を拓いたのだろうか。
そのプロセスを改めて振り返ることにしたい。
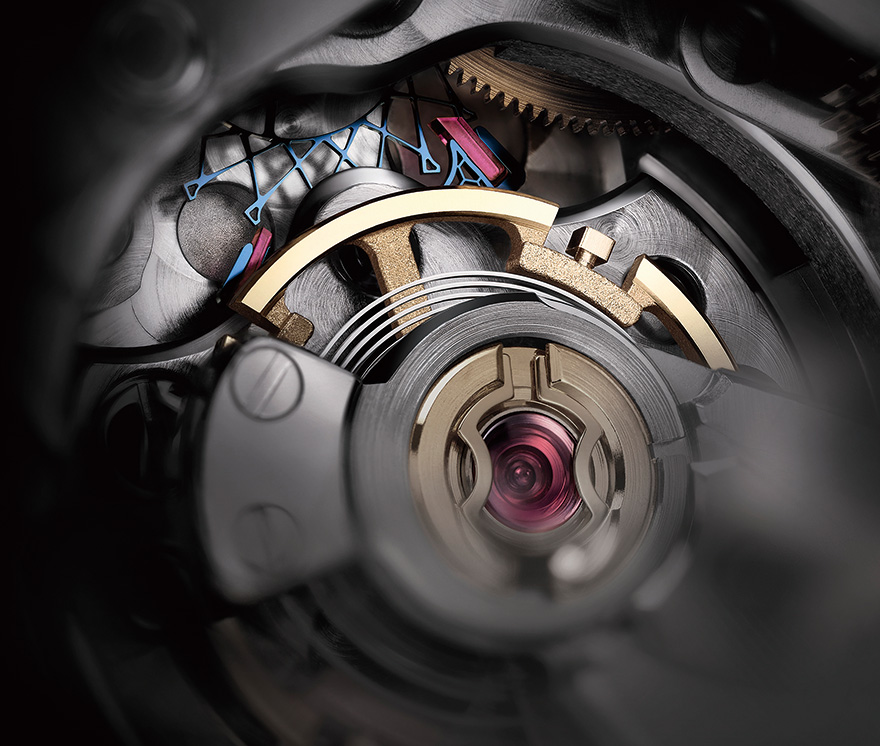
脱進機にシリコン素材を採用するメリットは何か。一般的には注油の必要がないことと考えられている。しかしより重要なのは、脱進機部品の軽量化によって、輪列のトルクロスが減少する点にある。つまりアンクルやガンギ車を鋼からシリコンに置き換えるだけで、ゼンマイのトルクを増やすことなく、より高い振動数か、より長いパワーリザーブを与えられるようになる。そのメリットは決して小さなものではないだろう。
シリコン脱進機のメリットに、最初に気付いたのはユリス・ナルダンであった。同社は重いデュアル・ダイレクト脱進機を改善するためシリコンの研究に着手。脱進機部品をシリコンに置き換えることで、この新しい脱進機は、ようやく実用性を得た。
対して、シリコン素材でスイスレバー脱進機を改善しようと考えたのは、スウォッチ グループ、パテック フィリップ、そしてロレックスの3社であった。ユリス・ナルダンと異なり、これら3社は開発当初からシリコン素材を量産機に載せることを目指していた。3社はヌーシャテルのラボラトリー「CSEM」にシリコンの研究を依頼。パテック フィリップは2005年、ブレゲは06年に、シリコン製のスイスレバー脱進機を備えたモデルを発表した。
両社は表向き、シリコン脱進機のメリットとして、注油の必要がないことを挙げてきた。しかし、本当の狙いはいささか異なるようだ。効率改善をパワーリザーブの延長に向けたのはパテックである。対してブレゲは、効率の改善を振動数の向上に充てようとしている。好例は、2011年のタイプXXIIだろう。
ブレゲが所有するラボラトリーの責任者は、シリコンパーツのメリットを次のように挙げる。「精密であること、軽いこと、磁力に強いこと、そして摩耗しないこと」。彼は、ここ数年でブレゲの精度が向上した理由は、シリコン脱進機のおかげだとさえ明言する。
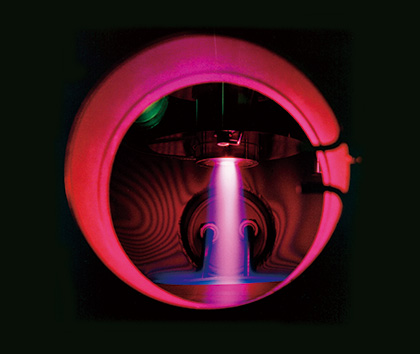
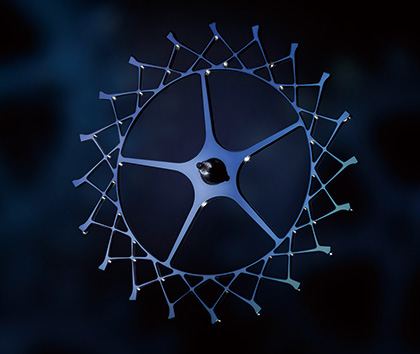
しかし、その実用化は決して順当に進んだわけではない。いくつかの課題は、シリコンを脱進機に用いることを阻み続けた。ひとつは割れやすい点。シリコン自体はかなり安定した素材だが、突起物に当たると容易に割れてしまう。以前ユリス・ナルダンの時計師が漏らしたように「ピンセットで触っただけで砕ける場合もある」ほど脆かったのである。もうひとつは、低温時の温度特性が良くなかった点だ。また、急激な温度変化にさらされた場合も、温度特性に優れるとは言い難かった。その点では、割れないうえ、温度特性も予想しやすい鋼のほうが素材としては扱いやすいだろう。また、水分を吸収しやすいシリコンの性質も、ムーブメント部品としては、適切なものとは思われなかった(もっとも吸水性をどこまで深刻な課題とみなすのかは、メーカーによって見解が異なる)。
対してCSEMと3社はシリコンの研究を続け、やがてその特性を改善した。CSEMはその詳細を明らかにしないが、「かつてのシリコンと現在のシリコンは性質が大きく異なる」という同社のコメントは、掛け値無しに信じて良いだろう。少なくとも、その温度特性が改善されなければ、ブレゲやパテック フィリップはシリコン製のヒゲゼンマイを採用しようと思わなかったはずである。
しかし、シリコンの研究を行ったCSEMはラボラトリーであり、素材の大量生産はできない。特性の改善をふまえて、スウォッチ グループは生産ラインを含めたシリコンのノウハウを傘下のニヴァロックス・ファーに移転するよう要請した。技術移転を推し進めるCSEMはこれを快諾(同様にCSEMと研究を続けていたユリス・ナルダンも、シリコン部品を製造するシガテックを設立)。信頼性の改善は、シリコン脱進機の量産に道を拓くことになった。05年、ニヴァロックスはヌーシャテル近くのマリンで、シリコン製造の研究を開始(おそらくこれにCSEMが一枚噛んでいる)。
08年の時点で、年間5万個のシリコン製部品、うち4万本のヒゲゼンマイを生産するようになった。生産の増加を受けて、ニヴァロックス・ファーは製造拠点をフォンテーヌに移転。以降ブレゲは、ヒゲゼンマイだけでなく、脱進機のシリコン化も推し進めてきた。その成果が、2010年に発表されたタイプXXIIだろう。これはベースムーブメントを大改造することなく、またパワーリザーブをさほど短くすることなく、7万2000振動/時という超高振動を実現したクロノグラフである。仮に脱進機を軽くせずに、同様の振動数を与えたければ、理論上は主ゼンマイのトルクを6.2倍以上に高める必要がある。主ゼンマイを大きく変えないまま振動数を上げられた理由は、いうまでもなく、比重が軽く、駆動効率を改善するシリコン脱進機にあった(もっともテンワの直径を小さくし、パワーリザーブを若干短くする必要はあった)。
また、注油の必要がないシリコン脱進機は、タイプXXIIのような超高振動機にはいっそうのメリットがあった。一般的には、振動数を上げれば上げるほど、ガンギ歯の油は飛散しやすくなる。とりわけ超高振動機の油は、ガンギ歯に油溜まりなどがない場合、一年も保たないといわれている。脱進機を完全無注油のシリコンに変えるだけで、長期的な精度が劇的に安定するのである。
タイプⅩⅩ規格が目指した高精度なクロノグラフという狙いは、約半世紀後のタイプXXIIでやっと実現することになる。タイプⅩⅩ規格が本当の意味で日の目を見るには、約半世紀もの歳月と、劇的な技術革新が必要だったのだ。